مل به قدمت مهندسی لاستیک
مهندس حیدری: نوآوری را جایگزین رقابت کردهایم.
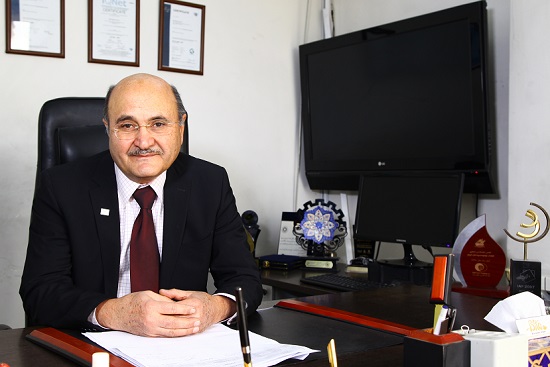
شرکت "مهندسی لاستیک" با نام اختصاری "مل" در سال ۱۳۵۹ با هدف تولید قطعات لاستیکی آغاز به فعالیت نمود. در سال ۷۸ همزمان با توسعه و رونق صنعت قطعهسازی در داخل کشور، با تجهیز مجدد واحد پرسکاری و قالبسازی ظرفیت تولید خود را به 3 برابر میزان سابق یعنی در حدود ۶۰۰ تن درسال رسانید. تخصص و دانش فنی مهندسین در شرکت به نوآوری و طراحی محصول جدید متمرکز شده و به عنوان یکی از بزرگترین تولیدکنندگان لاستیک در ایران توانستهاند بخش عظیمی از نیاز صنایع داخلی را تامین کنند. هماکنون شرکت مل با تولید بیش از۱۲۰۰تن محصولات لاستیکی درسال بزرگترین تولیدکننده قالبهای لاستیکی موزائیک ویبره درایران و اولین صادرکننده این محصولات به کشورهای حوزه خلیج فارس، کشورهای همسایه و همچنین کشورهای تازه استقلالیافته اتحاد جماهیر شوروی (سابق)، هندوستان، آمریکا، آفریقا و اروپا میباشد. |
در سالهای اخیر شرکت مل با بیش از نیم قرن تجربه با توسعه ماشینآلات تولیدی و تجهیزات آزمایشگاهی و نیز با تکیه بر تجربه متخصصان زبده، ظرفیت تولید سالانه خود را به 2 هزار و 400 تن در سال رسانده است.
این شرکت در قالب مجموعه 90 نفری در سه شیفت کاری و به طور شبانهروزی، با استقرار سیستم مدیریت کیفیت ISO/TS 16949-2009 توانایی تولید انواع قطعات لاستیکی مورد نیاز مشتریان در صنایع مختلف اعم از خودروسازی، ساختمان، ریلی، پتروشیمی، کشاورزی، لوازم خانگی، نفت، گاز و ... شامل انواع گردگیر، اورینگ، نوار، لوله، کاسه نمد، پکینگ، دیافراگم، قطعات لاستیک به فلز، انواع شلنگهای رادیاتور و بخاری خودروهای سبک، سنگین و... را داراست. در حال حاضر عمدهترین فعالیتهای شرکت مل در زمینه تولید انواع دیافراگم، دستگاه بادی پلاستیک، قطعات پرسی، قطعات اسفنجی، کامپاندسازی، پرسهای هیدرولیک، شیلنگهای مسلح و ... است.
توسعه فعالیتهای شرکت مل در زمینه طراحی و تولید قطعات لاستیکی و پلاستیکی مرهون ایجاد زیرساختهای مهندسی و کنترل کیفیت در این شرکت است. مهندس ناصر حیدری مدیرعامل شرکت مهندسی لاستیک را بر عهده دارد. آنطور که میگوید این روحیه کارآفرینی را از پدرش آموخته و از 9 سالگی وارد بازار کار شده است. روحیهای که در تمام سالهای حضور ایشان در صنعت نه تنها کمرنگ نشده همواره پرتوانتر و قدرتمندتر از گذشته زمینهساز خلاقیتها و فعالیتهای ایشان بوده است.
از 9سالگی وارد حوزه تجارت شدم
مهندس حیدری در معرفی خود و چگونگی ورودش به عرصه صنعت میگوید: در خانوادهای متوسط از نظر مالی ولی غنی از نظر فرهنگی به دنیا آمدم. پدرم از همان ابتدا روحیه استقلال و خودباوری را در ما پروراند. همۀ تابستانها کار میکردم و از همان تابستانهای کودکی و نوجوانی وارد حوزه کار و تجارت شدم. تابستانها کار میکردم و هزینه تحصیلم را پسانداز میکردم. آن زمانها کلاس کنکور و کلاس زبان بود اما من به دلیل تنگناهای مالی در آن کلاسها شرکت نمیکردم. همیشه از شاگردان زرنگ مدرسه بودم. در سال 48 در رشته مهندسی شیمی دانشگاه شریف قبول شدم.
در دوران تحصیل، کار میکردم و درس میخواندم. پس از فارغالتحصیلی و گذراندن خدمت سربازی، در جستوجوی کار بودم. بعدها درخواست پذیرش استرالیا دادم و پذیرفته شد اما دوری از خانواده و نگرانیهای مادرم نگذاشت به استرالیا بروم و اینگونه شد که سرنوشت من در همین کشور رقم خورد.
اولین بار به استخدام ایران یاسا درآمدم. خاطرم هست برای مصاحبه نزد مهندس صدیق رفتم. سابقه کار و تجربه حرفهای نداشتم و این موضوع پذیرشم را با دشواری روبه رو میکرد. اما پیگیریهای بسیاری کردم؛ به نظرم رمز موفقیت همین نکته است. پیگیری و دنبال کردن کارها تا رساندن به هدف نهایی!
ابتدا مدیر آزمایشگاه بودم اما کار خاصی بلد نبودم. خوشبختانه کارکنانی بودند که با جان و دل کار را به من یاد میدادند و من شبانهروز از آنها میآموختم. من سابقه همکاری با افراد بزرگی مثل آقای مهندس صدیق، مهندس یزدان حیدری، مهندس ثانی که همگی از کارآفرینان فعلی در صنعت هستند، را داشتم. که از انها بسیار آموختم. پس از مدتی با سِمَت معاونت به واحد تولید و خط تولید تایر تیوپ، منتقل شدم و مدتی پس از آن نیز رئیس تایر تیوپ ایران یاسا شدم.
ورود به بازار خارج به راحتی ممکن شد
پس از یک سال آن شرکت را ترک کردم. با دست خالی دو ماشین پرس کوچک خریدم و کارگاهی را راهاندازی کردم. پس از مدتی به راهنمایی دوستانم کارخانهای در کاشان راهاندازی کردیم. 20سال سهامدار عمده آن کارخانه و 10سال مدیرعامل آنجا بودم. در کنار مسئولیتهای مدیریتی فعالیتهای زیادی در بخش فنی آن مجموعه داشتم. بسیاری از ماشینآلات و تجهیزات فنی خط تولید را طراحی کرده و ساختم. اما فرهنگهای کاری متفاوت دستاندرکاران آن شرکت مانع ادامه همکاری من در آنجا شد. معتقدم سهامدار و مدیر عامل یک کارخانه، آن کارخانه را به یادگار میگذارد و من نیز آن کارخانه را در کاشان یادگاری گذاشتم و از آن مجموعه جدا شدم. متاسفانه روحیه همکاری در ایران ضعیف است. ما اصول شراکت و کار در کنار یکدیگر را بلد نیستیم.
سال 58 کارخانه لاستیک مل در سعیدآباد افتتاح شد. در همان ابتدای کار حادثه آتشسوزی بزرگی در کارخانه مل اتفاق افتاد. هنوز به شرایط کاملاً مساعد نرسیده بودیم که این اتفاق شرایط را سختتر کرد. پس از آن سایتی را از کمیته امداد امام خمینی اجاره کردیم و با انگیزهتر از قبل از نو شروع کردیم. سال 82 به طور رسمی وارد فضای فعلی شدیم. بازار خارج را با مذاکره حضوری و به راحتی باز کردم. از همان سال 82 شلنگسازی و ساخت قطعات پرسی را آغاز کردیم. از تراکتورسازی تبریز آغاز و سپس قطعات مورد نیاز را برای ایرانخودرو دیزل، ابکو، گروه بهمن، سابکو و سازهگستر تولید کردیم. اینگونه شد که قطعهساز خودرو شدیم. با این اعتقاد که یک کارخانه موفق نمیشود مگر آنکه صادرات داشته باشد همزمان با توسعه بازار داخلی بحث صادرات را هم با جدیت دنبال کردیم.
صادرات قالبهای موزائیک به کشورهای عربی، حاشیه خلیج فارس مثل قطر، کشورهای آسیای میانه، افغانستان و حتی استرالیا نیز داشتهایم.
همواره در حالِ تجهیز
مهندس حیدری به اهمیت آموزش تأکید دارد و میگوید: دورههای مدیریت را در شهر یوکوهوما در ژاپن گذراندم که در آن دوره به اهمیت سیستم پی بردم؛ دوره پلیمر در برگامو ایتالیا نیز دیدگاههای جدیدی به من داد. دورههای داخلی بسیار زیادی را در مراکز مختلف از جمله مرکز تحقیقات لاستیک و با اساتید بزرگی همچون دکتر ملایری گذراندم و همواره به فکر ارتقای دانش خود بودم. این تفکر در سایر بخشهای مجموعه جاریست.
وی بیان میکند: معتقدم هنگام تولید، ابتدا باید ابزار کار را فراهم کنیم؛ تأیید آزمایشگاه را بگیریم؛ مدارک را تکمیل کنیم و سپس شروع کنیم؛ زیرا روندی غیر از این، حاکی از تولید معیوب است.
«نوآوری» را جایگزینِ «رقابت» کردهایم
وی در این خصوص که چه برنامهای برای توسعه بخش آزمایشگاه، زیرساختهای کیفی و مهندسی و واحد تحقیق و توسعه شرکت مل دارند، میگوید: اگر مشکلات نقدینگی حل شود، قطعا شرایط بهتری برای کارخانههای تولیدی و سازندگان تجهیزات و ماشینآلات رقم میخورد. اما متاسفانه این مشکلات نقدینگی بر روی کیفیت نهایی هم به صورت کاملا ناخواسته تاثیرگذار است. بدون شک طراحی و تولید محصول با کیفیت و استاندارد هدف اصلی برای یک سازنده و تولیدکننده است اما برای این موضوع باید تجهیزات بهروز و مدرن داشت. برای بهروزرسانی تجهیزات و ماشینآلات خط تولید، آزمایشگاه یا کنترل کیفیت یکی از اساسیترین مسائل بحث نقدینگی و مالی است. واحدهای تولیدی متاسفانه از هیچ حمایتی در این بخش برخوردار نیستند.
با تمامی این مشکلات همواره در حال توسعه ماشینآلات، دستگاههای خطوط تولید و بخشهای مختلف آزمایشگاه هستیم. در برنامه آینده آزمایشگاه میخواهیم مجموعه کامل آزمونهای شلنگ را اضافه کنیم. در برخی آزمونها و عملکردها تأییدیه متد خودروسازان را گرفتهایم. در حال حاضر تولید این شرکت به ویژه در بحث شیلنگسازی افزایش چشمگیری یافته است. معتقدیم فقط با رقابت راه به جایی نمیبریم بلکه باید نوآوری کرد؛ برای نوآوری در صنعت باید تمام جوانب و ابعاد آن را بشناسید. باید کم و کاستیهای محصول، نقاط قوت آن و البته نیاز بازار را بشناسید. باید برای طی کردن مسیر و رسیدن به هدف زمان بگذارید. تحصیلات دانشگاهی و آکادمیک بسیار پسندیده است اما قطعا کافی نیست. بخشی از دانش که راهگشای مسیر و پدید آورنده ایده های جدید است در خلال سالها کار و تجربه به دست میآید.
مهندس حیدری در این خصوص که آیا تصمیم دارند محصولات دیگری به سبد تولیدات خود اضافه کنند، میگوید: ما همواره در اندیشۀ افزایش تولیدات و نوآوری در طراحی هستیم و به طور مداوم به دنبال ایدههای جدید هستیم. زمانی که ما در ابتدای کار شروع به طراحی پردههای دیافراگم گازی کردیم، این پردهها کاملا وارداتی بودند. ما در آن دوران توانستیم با اختلاف قیمت بسیار با نمونه خارجی این محصول را برای اولین بار طراحی کرده و به مرحله تولید برسانیم. از آن روز و تاکنون این روند همواره وجود داشته است. نوآوری و طراحی محصول جدید همواره در نظر ما بوده است.
شاید با تکیه بر همین ویژگی امکان صادرات محصول برای شرکت مل میسر گردید. زیرا محصول جدید با ویژگیهای جدید همیشه بازار مخصوص خود را دارد. در همان سالهای اولیه حتی توانستیم محصولاتی را به کشور هندوستان که در صنعت لاستیک بسیار موفق و پیشرو هست، صادر کنیم. نوآوریهای خاصی هم در زمینه طراحی برخی مواد خاص با کاربردهای ویژه برای صنایع نظامی داشتیم. تا زمانی که بتوانیم برای طراحی محصول جدید نوآوری و ایده نوین داشته باشیم، مسیر پیشرفت و موفقیت در صنعت لاستیک برای مجموعه مهندسی لاستیک مل مهیاست.