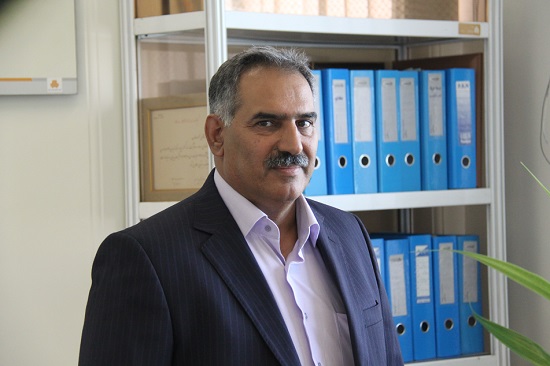 |
مهندس محمود طالب
معاونت مهندسی شرکت سازهگستر سایپا
|
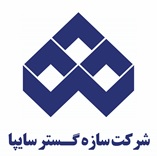
انجام آزمونهای محصول اولین پایه تحقق خواستههای مشتری است. بدون داشتن آزمایشگاه مجهز، تجهیزات مناسب، دقیق و استاندارد، عملاً امکان اثبات کیفیت محصول و رعایت الزامات مشتری فراهم نمیگردد.
مهندس طالب دارای مدرک مهندسی مکانیک از دانشگاه صنعتی شریف و کارشناسی ارشد مدیریت کسب و کار (MBA) هستند. ایشان با سابقه بیش از 15 سال حضور مستمر در بدنه مدیریت گروه خودروسازی سایپا اکنون به عنوان معاونت مهندسی شرکت سازهگستر سایپا مشغول به فعالیت هستند. همچنین مدیریت امورهای مهندسی تکوین، مهندسی متد و مهندسی محصول از زیرمجموعههای این معاونت است. با توجه به این که از یک سو با توسعه محصولات گروه خودروسازی سایپا و نوآوری در خودروهای جدید مواجه بوده و از سوی دیگر در شرایط پساتحریم، باز شدن افق همکاری با کشورهای صنعتی، ورود فناوریهای نوین و سیاستهای توسعهنگر دولت در ایجاد تنوع کمی و کیفی در صنایع خودروسازی را شاهد هستیم؛ نقش معاونت مهندسی شرکت سازهگستر اهمیتی دوچندان یافته است.
فرصتی ایجاد شد تا در فضایی صمیمانه با مهندس طالب درباره سازوکار معاونت مهندسی سازهگستر، برنامههای پیش رو، پروژههای اجرا شده و در دست اجرا و نقش مهندسی متد در طراحی، تکوین و کیفیت محصول گفتوگو کنیم.
در طول 15 سال سابقه حضور شما در گروه خودروسازی سایپا؛ مدیریت چه پروژههایی به عهده شما بوده است؟
تقریباً درتمام خودروهای جدید مدیر پروژه بودهام. مهمترین محصول تحت مدیریت بنده تیبا بود که مدیر پروژه سازهگستر آن بودم. اکنون هم تمام طرحهای خودرویی در حوزه کار معاونت مهندسی قرار میگیرد.
لطفاً نقش، جایگاه و برنامههای معاونت مهندسی شرکت سازهگستر را شرح دهید.
گروه سایپا، دو تامینکننده اصلی دارد. شرکت مگاموتور و شرکت سازهگستر؛ که بخش عمدهای از قطعات و مجموعهها، تحت مدیریت و نظارت این دو شرکت تولید و تامین میشوند. در شرکت سازهگستر 65 تا 70 درصد قطعات انواع خودروها تامین میگردد. این شرکت متشکل از معاونتهای مختلفی است که بنده در حوزه مهندسی مشغول به فعالیت هستم. معاونت مهندسی شرکت سازهگستر دارای سه حوزه مدیریت مهندسی تکوین، مهندسی محصول و مهندسی متد است.
نقش ما مدیریت مهندسی زنجیره تامینکنندگان است. طراحی قطعات یا در زنجیره تامینکنندگان انجام میشود یا در بخشهای بالاتر، ولی هیچ قطعهای را در سازهگستر طراحی نمیکنیم. طراحی قطعات امری تخصصی است که معتقدیم باید در بدنه زنجیره تامین صورت گیرد . طراحی کلان خودرو مسوولیت خودروساز و واحدهایی مانند مرکز تحقیقات و نوآوری سایپا (AIRIC) است. وظایف معاونت مهندسی شرکت سازهگستر عبارتنداز: به کارگیری روشهای سیستماتیک جهت امکانپذیری اجرا، برنامهریزی، کنترل و تصدیق فرایند ساخت محصولات طراحی شده، بازنگری طرحها و ارائه پیشنهادات اصلاحی در مطابقت با مراجع معتبر مانند استانداردها و نقشههای فنی، بررسی و کسب اطمینان از کامل بودن نقشههای فنی و استانداردهای محصول، تبیین ویژگیهای عملکردی محصول، بررسی تغییرات متناسب با الزامات کیفی مشتریان، گزینش سازندگان بالقوه با توجه به فاکتورهای مدون، تحلیل اولیه جهت کاهش هزینههای ساخت و اجرا، مدیریت طراحی، کنترل و تصدیق ابزارهای تولیدی، آزمون و اندازهگیری.
ارتباط این نهاد با مهندسی سایپا و سایر شرکتهای زیر مجموعه چگونه است؟
واحدهای مهندسی مرکز تحقیقات، سایپا و سایر شرکتهای گروه سایپا با یکدیگر تعامل دارند؛ چه از نظر بحثهای تکوین قطعات و محصولات و چه از بُعد تدوین مدارک و ساخت تجهیزات با یکدیگر در ارتباط هستند. بسیاری از نکات طراحی و ساخت به صورت گروهی و تعاملات مهندسی مشترک به انجام میرسد.
در حال حاضر چه پروژه¬هایی را در دستور خود کار دارید؟
پروژههای جدیدی مانند پروژه 211 ، 232 و همچنین پلتفرمهایی مانند Z100 و SP100 و SP0 در حال انجام است. این پروژهها از اهمیت ویژهای برخوردار است چراکه با برند سایپا تولید خواهد شد. برخی محصولات دیگر متعلق به سایر برندهاست که در ابتدا به صورت (CKD (Complete Knock Down وارد و تولید میشوند. پیشبینی میشود در چرخه عمر این محصولات تا سی درصد قطعات به خودکفایی برسند.
شما مدیر پروژه مهمترین محصولات سایپا در شرکت سازهگستر هستید. همان طورکه استحضار دارید تجهیزات آزمون و آزمایشگاههای تخصصی در ارتقای کیفیت محصولات، نقش بسیار موثری دارند. لطفاً بفرمایید که در گروه سایپا و در حوزه تامینکنندهها چه برنامهای برای توسعه زیرساختهای آزمون دارید؟
نقش اساسی شرکت سازهگستر مدیریت زنجیره تامین است که متولی تامین قطعات مطابق مشخصات مهندسی در زمان معین با قیمت مناسب و به خصوص منطبق با کیفیت تعریف شده است که عموماً بالاترین استانداردهای مطرح هستند. رسیدن به کیفیت، رسالت اصلی، اولویت اول کاری ما و غیر قابل عدول است. اگر قطعهای بدون کیفیت تولید شود مانند آن است که کاری انجام نشده است. پس کیفیت و کسب آن صدر دستور کار همه گروههای سازهگستر است. برای اطمینان از اینکه به کیفیت مورد نظر مشتری رسیدهایم، اولین گام انجام آزمونها مطابق با مدارک محصول و طرح آزمون (Test Plan) سفارشدهنده است. بنابراین انجام آزمونهای محصول اولین پایه تحقق خواستههای مشتری است. این فرآیند جایگاه و نقش آزمایشگاههای تخصصی و تجهیزات مربوطه را به روشنی مشخص میکند. بدون داشتن آزمایشگاه مجهز، تجهیزات مناسب، دقیق و استاندارد، عملاً امکان اثبات کیفیت محصول و رعایت الزامات مشتری فراهم نمیگردد.
رسیدن به کیفیت، رسالت اصلی، اولویت اول کاری ما و غیر قابل عدول است.
در پروژههای مختلف بسته به نوع آزمونها، تجهیزات و میزان سرمایهگذاریها، امکانات و برنامههای انجام آزمونها تبیین میگردند. برخی از آنها با توجه به امکانات و شرایط موجود، در آزمایشگاه سازهگستر انجام میشود، برخی در آزمایشگاه سازندگان و تعدادی هم در آزمایشگاههای مستقل و معتبر بیرون از گروه سایپا انجام میپذیرد.
برهمین اساس، در شروع اجرای پروژه، آزمونهای مرتبط طرحریزی و مراکز انجام آنها تعیین و تقسیمبندی میشوند؛ لذا در هر پروژه برنامه زمانبندی مشخص شده است و مطابق آن مسوولین هر قطعه باید برنامهریزی انجام آزمونها را طرحریزی نمایند. بعضی آزمونها تنها یک بار در زمان طراحی محصول و برخی دیگر به صورت مستمر به انجام میرسند. معمولاً سعی بر این است در آزمونهای مستمر جهت دسترسی بهتر و پرهیز از اتلاف وقت و هزینه، سازهگستر یا سازنده، تجهیزات و امکانات آزمونهای لازم را فراهم کنند. یکی از وظایف معاونت مهندسی در امور مهندسی متد، تامین بخشی از تجهیزات و نظارت و صحهگذاری عملکرد آن هاست؛ به خصوص اگر تجهیزات، خاص باشند. بدان معنا که این تجهیزات صرفاً جهت انجام یک آزمون خاص عملکردی یا دوام یک محصول خاص طراحی و ساخته میشوند.
انجام آزمونهای محصول اولین پایه تحقق خواستههای مشتری است. بدون داشتن آزمایشگاه مجهز، تجهیزات مناسب، دقیق و استاندارد، عملاً امکان اثبات کیفیت محصول و رعایت الزامات مشتری فراهم نمیگردد.
اغلب خودروسازهایی که در ایران مشغول به فعالیت هستند همین شیوه را دنبال میکنند؛ اما این نگرش در جزئیات، حواشی و مسائل جانبی متعددی دارد. مثلاً بخش عمدهای از قطعهسازان آزمایشگاهی دارند که صرفاً تجهیزات ضروری آزمون را تهیه کردهاند و البته همه دستگاههایی هم که در اختیار دارند لزوماً تطبیق کامل با استاندارد را ندارند. اگر همه چیز ایدهال بود، مشکل کیفی نداشتیم. در این مقوله دیدگاه شما چیست؟
شما با این حوزه کاملاً آشنایی دارید. موضوعی را که مطرح کردید گستردهتر از یک مصاحبه معمولی است؛ بنده بخشی از نظرات شما را قبول دارم. ما کار بدون کیفیت انجام نمیدهیم. ولی نکته قابل تامل این است که کشور ما در حال رشد است، صنعت خودروی ما هم پایه و پیشینه کمی دارد. شاید نزدیک به دوازده سال است که به صورت جدی ساخت داخل را آغاز کردهایم. قبل از آن مونتاژکار بودیم و با روش کپی کردن پیش میرفتیم. به تازگی درگیر موضوعات پیچیده تر شدهایم. هرچه پیش میرویم خواستههایمان عمیقتر میشود. یعنی اگر آن محصولی که امروز از سازنده میخواهیم در گذشته هم خواسته بودیم؛ یقیناً انجام میداد. ما دیروز نمیخواستیم؛ چون نمیدانستیم، یاد نگرفته بودیم. صنعت خودرو روز به روز در حال گسترش است. پیشرفتهایی رخ میدهد. خواستههای مصرفکننده بیشتر میشود. برنامههای کنترل کیفی مشتریان ما نیز هرروز دقیقتر و گستردهتر میشود. ما پا به پای مشتریان، پا به پای دنیا حرکت کرده و خود را به روز میکنیم. فکر نمیکنم هیچ روزی، قطعهای را بدون کیفیت تولید کرده باشیم. مگر اینکه تعریف ما از آن قطعه در آن روز چیز دیگر بوده باشد و امروز چیز دیگر. قطعا خودرویی که امروز تولید میکنیم و آزمونهایی که امروز بر روی قطعات انجام میدهیم با سالهای پیش تفاوت دارد. به دلیل اینکه استانداردها، الزامات و حتی تجهیزات، همگی تغییر کرده و خواستهها نیزعوض شدهاند. ما هم خودمان را با شرایط سازگار میکنیم. لذا از لحاظ کیفی رو به جلو و بهبود هستیم ولی هرگونه تطبیقی به زمان نیاز دارد.
به عنوان مثال در طراحی خودروی جدید نیاز به ادوات و تجهیزات آزمون جدید داریم. تامین این تجهیزات به دلیل تغییرات استاندارد و الزاماتی که در کشور رخ می دهد هزینهبر و زمانبر است؛ با این وجود هیچ یک از عوامل زنجیره تامین از کیفیت عدول نمیکنند. تکتک اجزای زنجیره تامین تحت کنترل است. به بخش فروش محصولات نگاه کنید؛ کمترین میزان نارضایتی مشتری نسبت به حجم تولید و عرضه محصول را ما داریم. حواشی موجود خیلی بیشتر از اصل موضوع است. همین الان اگر به تعمیرگاههای خودروهای وارداتی سری بزنید مشاهده خواهید کرد که میزان نارضایتی در آنجا بسیار بیشتر از محصولات ماست. اولین دلیل آن این است که در ساخت داخلِ برخی از قطعات مورد نیاز با توجه به دشواری تامین و خرید از منابع خارجی، حساسیتهای واحدهای مهندسی در طراحی و ساخت محصولات بالا رفته و کیفیت تولیدات متناسب با آن ارتقا یافته است. دومین دلیل؛ رشد کیفی محصولات داخلی با توجه به عمق تجارب چندین سالهای است که در بدنه خودروسازی و همچنین در زنجیره تامین شکل گرفته است. نمونه بارز آن، مقایسه کیفیت قطعات تولیدی ما با نمونههای چینی است که از کیفیت بسیار بالاتری برخوردارند؛ و دلیل آن هم این است که قطعات چینی قابلیت برآوردهسازی آزمونهای ما را که مطابق با استانداردهای روز تدوین گشتهاند، ندارند. همانگونه که به آن اشاره کردم بیشترین تمرکز ما سازگاری با تغییراتی است که به دلیل افزایش انتظارات مشتریان به تدریج رخ میدهند. مانند پروژههای جدید که برنامه منسجم و جامعی در ساخت قالبها، ابزارهای کنترلی و تجهیزات آزمون تهیه کردهایم تا این خلأ را به حداقل ممکن برسانیم.
فکر نمیکنم هیچ روزی، قطعهای را بدون کیفیت تولید کرده باشیم. مگر اینکه تعریف ما از آن قطعه در آن روز چیز دیگر بوده باشد و امروز چیز دیگر. قطعاً خودرویی که امروز تولید میکنیم و آزمونهایی که امروز بر روی قطعات انجام میدهیم با سالهای پیش تفاوت دارد. به دلیل اینکه استانداردها، الزامات و حتی تجهیزات، همگی تغییر کرده و خواستهها نیزعوض شدهاند. ما هم خودمان را با شرایط سازگار میکنیم. لذا از لحاظ کیفی رو به جلو و بهبود هستیم ولی هرگونه تطبیقی به زمان نیاز دارد.
همان گونه که مستحضرید یکی از مشکلات عمده سازندگان نداشتن امکانات آزمایشگاهی و تجهیزات آزمون خاص است و آن هم به دلیل ناکافی بودن درآمد این حوزه و هزینه بالای تامین و به روزرسانی ادوات و تجهیزات است. لذا آن ها سعی میکنند بسته به نیازهای مبرم و ضروری خود اقدام به تهیه تجهیزات نمایند. برنامه شرکت سازه گستر جهت پوشش کلیه آزمونهای مورد نظر قطعات و محصولات جدید چیست؟
در حال حاضر سازندگان نمیتوانند در توسعه آزمایشگاه و تجهیزات، سرمایهگذاری سنگین کنند؛ اما طبق قراردادی که با ما دارند بخشی از این تجهیزات مانند تجهیزات عمومی یا فیکسچرهای کنترلی (CF - Checking Fixture) را خودشان تامین میکنند. ولی به آزمونهای خاص که میرسند، قادر به سرمایهگذاری نیستند. از طرفی سرمایهگذاری موازی سازندگان با یکدیگر منطقی نیست. اینجاست که وجود آزمایشگاههای مستقل که پاسخگوی نیاز آن ها باشند اهمیت مییابد. سالهای قبل هم شرکتهایی مانند ایتراک به همین دلیل به وجود آمدند. وجود چنین آزمایشگاههایی چندین فایده دارد: حجم سرمایهگذاری کاهش مییابد، انجام آزمونها به شکل تخصصی و دقیقتر صورت میپذیرد و در نهایت زمانی که مرجع سومی آزمونها را مستقل از واحدهای درخواست دهنده انجام دهد؛ اطمینان بیشتری را به مشتری و خودروساز میبخشد.
یکی از کمبودهایی که الان در صنعت داریم تعداد آزمایشگاههای مستقلی است که بتوانند برای صنعت خودرو سرمایهگذاری کرده و براساس استانداردهای روز تجهیزات آزمون را فراهم کنند. تا زمانی که منتظر سازنده و قطعهساز باشیم تا آزمایشگاه تخصصی را ایجاد نماید با توجه به حجم سرمایهگذاری بالا عملاً زمان را از دست میدهیم در حالی که هیچ آزمایشگاهی ایجاد نخواهد شد. برای تاسیس یک مرکز آزمون جامع، معتبر و مستقل باید یک سازمانی وابسته به صنایع بزرگ، وزارتخانه ها، ارگانها و شرکتهای دولتی دیگر این کار را انجام دهند. در کشورهای توسعه یافته نیز به همین صورت است. بسیاری از خودروسازان با وجود توان مالی که دارند باز ترجیح می دهند یک شریک سومی را برای انجام آزمونهای خود داشته باشند.
بیشترین تمرکز ما سازگاری با تغییراتی است که به دلیل افزایش انتظارات مشتریان به تدریج رخ میدهند.
در طراحی آزمونها و توافقاتی که با سازندگان انجام میشود، سازنده چه آزمونهایی را باید در داخل مجموعه داشته باشد و چه آزمونهایی را مجاز است از خدمات خارجی استفاده کند؟
شرکتها ممکن است دو ماهیت متفاوت داشته باشند. میتوانند قطعهساز یا طراح باشند. به تناسب ماموریتی که دارند تجهیزات تست مورد نیاز خود را هم باید فراهم کنند. در گام بعدی، باید دید که آن تجهیزات چه میزان مصرف و چه هزینهای دارند. آیا سرمایهگذاری بر روی آنها توجیه دارد یا خیر. اگر سرمایهگذاری توجیه دارد هر سازنده میتواند برای خودش این تجهیزات و فضای آزمایشگاهی را فراهم کند که اغلب اینگونه نیز هست. درغیر این صورت باید یک شرکت مرجع، شبکهای از آزمایشگاههای تخصصی را تجهیز نموده و متولی انجام آزمونها شود. از لحاظ نوع بهرهبرداری نیز میتوان به این موضوع پرداخت؛ تجهیزات و ادوات مربوط به آزمونهای روزانه و حین فرآیند تولید باید توسط سازنده تهیه شوند و در داخل مجموعه مستقر باشند؛ چنین مواردی را نمیتوان به آزمایشگاه دیگری واگذار کرد. اما آزمونهای پرهزینه و بدون فوریت را میتوان از خدمات بیرون استفاده کرد.
به هرحال وجود آزمایشگاههای تخصصی و تجهیزات آزمون قطعی است. سازنده اگر آزمونی را به صورت مستمر انجام میدهد حتماً باید تجهیزاتش را نیز تهیه کند. برای هر تجهیزی فارغ ازآنکه در داخل مجموعه یا خارج آن انجام شود باید دقت عملکرد و صحت نتایج آنها صحهگذاری گردد؛ که این فرایند در زیر مجموعه معاونت مهندسی و توسط امور مهندسی متد انجام میشود.
یک تغییر عمده که بعد از حضور شما در سمت معاونت مهندسی شرکت سازهگستر رخ داد توسعه واحد مهندسی تکوین محصول بود. لطفاً در مورد نحوه شکلگیری و ساز و کار این واحد توضیح فرمایید.
مهندسی تکوین شرکت سازهگستر یک واحد جدید نیست. قدمت زیادی دارد. سالهای قبل به دلیل تعداد پروژههایی که داشتیم واحدهای تکوین و تامین گستردهتر از امروز وجود داشت. در واقع به تعداد واحدهای تامین، واحد تکوین داشتیم. ولی نام آنها، واحد ساخت بود. به مرور زمان با کاهش پروژهها واحدها کوچکتر و با هم ادغام شدند و ماموریت آنها یکی شد؛ بعد که دوباره سایپا استراتژی تنوع محصول را پیش گرفت، دوباره این نیاز احساس شد. واحدهایی که کار تامین مستمر را انجام میدهند فرصت نمیکنند به کار تکوین به صورت تخصصی بپردازند. ممکن است یک روز دوباره این واحدها ادغام شوند. با وجود آنکه واحدهای تامین ما واحدهایی هستند که کارهای مهندسی تخصصی انجام میدهند؛ اما اولویت کارشان پشتیبانی خطوط تولید است و نمیتوانند برای کارهای تکوین وقت بگذارند. روش کار ما این است که پروژه در امور تکوین آغاز و پس از طی مراحل طراحی و تهیه مدارک فنی؛ اثبات کیفیت و نهادینه شدن تولید در خط انبوه، جهت تولید مستمر به واحد تامین منتقل میگردد. مانند خودروی وانت 151 که سال گذشته و خودروی 211 در سال جاری و خودروی 232 که سال بعد به امور تامین منتقل میگردد. در واقع هیچ یک از پروژههای تکوین دائمی نیستند؛ بلکه پس از نهاییسازی و رفع مسائل و مشکلاتشان به تامین منتقل میشوند.
بنابراین توسعه واحد تکوین به سبب حضور من نبود؛ مقتضی زمان و متناسب با نیاز سازمان بوده است. البته شما درست میفرمایید. ما حدود 2 سال گذشته به تدریج واحدهای تکوین را بزرگتر کردیم. به دلیل اینکه تعداد پروژههایمان بیشتر شد و فعالیتهای پروژهای عمیقتر شد. در صورتی که توان طراحی هر قطعهای در زنجیره تامین شرکت سازهگستر وجود داشته باشد خودمان انجام میدهیم. پروژههای ما در سالهای قبل در حد خودروی 151 تا 211 بود. از اوایل سال 1393 که پروژه SP100 را شروع کردیم طراحی صفر تا صد آن با مسوولیت شرکت سازهگستر بوده است. در این پروژه اغلب سازندههایی که توان طراحی داشتهاند؛ به کار گرفتهایم.
البته پیچیدگی کار بیشتر شده است. ما در پروژههای قبلی حدود سی مورد طراحی داشتیم و بقیه کار را عمدتاً طراحی شده به دست سازندهها میسپردیم که بخش تکوین را انجام دهند. در پروژه SP100 بیست سازنده را درگیر کردیم. سازندگانمان توسعه یافته اند. میزان طراحهایی که امروز در زنجیره تامین داریم؛ پنج سال پیش نداشتیم. کمتر از این تعداد بودند. الان سازندگان امکانات خیلی خوبی دارند. جهتگیری ما به سمتی است که زنجیره تامین، کاملاً تخصصی کار کند. یعنی سازنده توانمندیها و قابلیتهایش را رشد و پرورش داده و تا جایی که قابلیت اعتماد و اتکا را به دست آورد. امیدواریم در بحث تجهیزات تست هم بتوانیم همین رویه را پیش بگیریم وموفقتر از قبل عمل کنیم.
از اوایل سال 1393 که پروژه SP100 را شروع کردیم طراحی صفر تا صد آن با مسوولیت شرکت سازهگستر بوده است. در این پروژه اغلب سازندههایی که توان طراحی داشتهاند؛ به کار گرفتهایم.
یکی از مباحث مهم در طراحی و مهندسی محصول به روز رسانی مدارک فنی و استفاده از استانداردهای روز دنیاست. اغلب این استانداردها متناسب با سطح فناوری استفاده شده در محصولات جدید یا حتی برخی از قطعات قدیمی نیستند. برنامه واحد مهندسی جهت به کارگیری استانداردهای جدید و ارتقای سطح آزمون ها چیست؟
بنده تنها بخشی از سخنان شما را قبول دارم. این ایرادها در مورد خودروهای قدیمی، مصداق دارد. به دلیل اینکه مدارک فنی محصول به صورت پراکنده و تدریجی از خودروسازهای دیگر برای ما میآمد و چون ارتباطات قطع شده بود قابل به روز رسانی نبودند. یعنی الان اگر بخواهید مطابق مدارک فنی گذشته تستی را انجام دهید، نقصها و مشکلات زیادی وجود دارد. ولی در پروژههای جدید، استانداردهایمان جدید و بهروز شدهاند. البته برخی مدارک نیاز به بازنگری دارند. در طراحی خودروهای جدید با طراحان خارجی در تماس هستیم؛ واحدهای تخصصی برای تایید مشخصات تست (test plan) و تعریف الزامات فنی وجود دارند که همه استانداردها، نقشهها و مدارک فنی را بهروز نگه میدارند. مثلاً در پروژه SP100 بر اساس استانداردهایی کار میکنیم که از سال 2017 به بعد در دنیا جاری خواهند بود؛ نه بر اساس استانداردی که امروز رایج است. به روشی کار میکنیم که قطعاتمان برای 15 سال بعد نیز بتواند بهروز باشد.
این تغییرات برای چه پلتفرمی اعمال میشود؟ آیا پلتفرمهای جدید را شامل میشوند؟
مطابق با استراتژی گروه سایپا بر روی پلتفرمهای قدیمی کار جدیدی انجام نمیشود. آنها متوقف خواهند شد. برنامه ما آن است که پلتفرمهای جدیدمان را در قالب همین پروژهها توسعه دهیم. یعنی خانواده محصولات سالِ 1395 به بعد با خانواده محصولات فعلی هیچ اشتراکی ندارند.
یکی از نشانههای ضعف مدارک فنی و استانداردهای تست عدم بومیسازی استانداردها و نقشههای آزمون قطعات است. اغلب استانداردها متناسب با شرایط اقلیمی کشورهای اروپایی نوشته شدهاند و برای شرایط ایران معنی نداشته، عملاً نیازی به آنها نیست. مثلاً آزمونهای شرایط جوی با رطوبت بالا در آنجا اهمیت بسیاری دارد؛ اما اینجا در ایران به خاطر وجود خاک و غبار آزمون گرد و غبار مهمتر است. اما نظام مهندسی ما چنین مواردی را بومیسازی نکرده است.
قطعاً مهندسین ما در شرکت سازهگستر و سایپا به این نکات در تدوین مدارک فنی توجه کرده و به آن ها پرداختهاند. در گروه سایپا وقتی بر روی پروژههای آتی کار میکنیم، همه موارد را با فناوری روز در نظر گرفته و تلاش میکنیم چنین مشکلاتی را برطرف کنیم. در خودروهای جدید قطعاً با نگاه به آینده و برای پانزده سال بعد مشخصههای تست (Test Plan) را تعیین و تجهیزات و محصولاتی را طراحی میکنیم. حتی اگر لازم باشد در این حوزه نیز سرمایهگذاری خواهیم کرد.
در پروژه SP100 بر اساس استانداردهایی کار میکنیم که از سال 2017 به بعد در دنیا جاری خواهند بود؛ نه بر اساس استانداردی که امروز رایج است.
سوالی که در این جا پیش میآید این است که در پروژههای جدید معیارهای مهندسی و استانداردهای جدید نیازمند ساختارهای مشخص و استانداردهای معتبر هستند. آیا این زیرساختها در مجموعه مهندسی شرکت سایپا و به تبع آن شرکت سازهگستر شکل گرفته است؟
بله، ساختاری برای این کار وجود دارد. مرکز تحقیقات و نوآوری سایپا (AIRIC) به عنوان متولی طراحی خودرو، واحد مهندسی سایپا به عنوان مشتری و واحد مهندسی سازهگستر و نماینده سازنده به عنوان طراح محصول در یک ساختار تعریف شده و در قالب یک تیم، مسوولیت طراحی محصول، تدوین مدارک فنی و نقشه هاو الزامات تست را بر عهده دارند.
آیا واحدهای ذکر شده هماهنگ هستند؟
بله؛ روش کار در پروژههای جدید به این صورت است که طراحان در زنجیره تأمین مسوولیت تهیه طرح اولیه محصول و ارائه نقشه آزمون (Test Plan) محصولات و قطعات مطابق با درخواست مشتریان و استانداردهای مربوط را بر عهده دارند. طرح اولیه در قالب گروههای مهندسی مورد بررسی و بازنگری قرار گرفته و تجربیات و دانش آنها بر روی آن سوار میشوند. در این مرحله مدارک فنی، نقشههای آزمون و معیارهای پذیرش محصول تعیین و مورد تأیید خودروساز، سازهگستر، مرکز طراحی و طراح پلتفرم قرار میگیرد.
خوشبختانه واحدهای مهندسی، نظارتی و واحدهای کیفی ما بر استانداردهای پیشرفته و الزامات روز دنیا تمرکز و تجربه کامل دارند. به همین علت بازنگریهای متعددی در فرآیندهای کیفی سازندگان و مشتریان صورت گرفته است. به تازگی یک نظام جدید کنترل کیفی در سطح گروه تعریف و بازنگری خاصی بر روی آن صورت پذیرفته است. یعنی اینکه ما اصرار داریم محصول با کیفیت و مطابق استاندارد روز تولید کنیم و هزینه آن را هم پرداختهایم. هزینههایی که میکنیم به این خاطر است که اصرار به کیفیت داریم.
نقش معاونت مهندسی در رفع مشکلات و شکایات مشتریان که از طریق واحدهای کنترل کیفیت سازمان مطرح میگردد چیست؟
در بعضی از موضوعات ما مسوول و در بعضی دیگر پشتیبان هستیم. در مورد رسیدگی به شکایت مشتریان سازندگان و قطعه سازان در مقابل مشتری قرار نمیگیرند. واحد مستقلی تحت عنوان واحد رضایت مشتری در معاونت کیفیت شرکت سازهگستر قرار دارد. آنها با مشتری ارتباط مستقیم دارند. نسبت به بازخوردها و گزارشاتی که از سوی آنها اعلام میگردد پشتیبانیهای لازم از سوی مهندسی انجام میشود. یعنی هرجا نیاز باشد برای بررسی موضوعات کیفی، علل اشکالات پیش آمده و یا حتی جبران، در خدمت تیمهای مرتبط هستیم. مثلاً اگر قطعهای دارای مشکل عملکردی باشد، مشکل را بررسی و متناسب با مدارک و اطلاعات فنی آن پاسخگوی نیازهای کیفی خواهیم بود.
موضوع تحریم در صنایع داخلی کشور به خصوص صنعت خودروسازی نقش مهمی داشته است. آیا شرکت سازهگستر توانسته است از تحریم به عنوان یک فرصت استفاده نماید؟
هدف تحریم ها اعمال فشار و فلج کردن صنایع داخلی بوده است. سختیها ناگزیر بودند ولی برای جبران این فشاری که از بیرون به ما میآید راهکارهایی پیدا و آنها را به فرصت تبدیل کردیم. در تجهیزات آزمون و ادوات اندازهگیری قطعاً وابستگیهای زیادی داشتیم. تهیه امکانات اندازهگیری، تجهیزات و مواد مصرفی در آزمایشگاهها سختتر شد. بنابراین در اولین گام اقدام به طراحی آنها کردیم. روشهای سادهتری را برای تامین آن تجهیزات و ادوات وابسته پیشبینی کردیم. به دنبال منابع در دسترس رفتیم. در برخی از موارد مجبور شدیم با صرف هزینه بیشتر بر مشکلات فائق آییم. نهایتاً برای اولین بار موفق به ساخت بسیاری از تجهیزات آزمون پیچیدهای شدیم که تا امروز در کشور وجود نداشت. در کنار این موضوع شرکتهایی به وجود آمدند که با اتکا به توان مهندسی بالای خود توانستند بخش عمدهای از محصولات و خدمات وابسته را خوشان تامین نمایند. مثلاً در آزمون شبیهساز نور خورشید که از نور زنو استفاده میشود. لامپی است با طول عمر محدود؛ قطعه مصرفی است و حتماً باید از نوع مرغوب استفاده شود؛ بنابراین هزینه و زمان زیادی برای آن صرف شد. در آزمایشگاه خودمان به واسطه عدم وجود لامپ مذکور گاهی تا دو ماه تستهایمان به تعویق میافتاد و پروژههایمان را متوقف میکرد. بنابراین در مواردی سازنده مجبور میشد طراحی کند و خود بسازد. اینجا بود که نقش واحدهای مهندسی ما در طراحی، ساخت و صحهگذاری بسیار اثربخش بود. خیلی از امکاناتی که امروز در صنعت خودرو داریم به این شیوه ایجاد شده است. مثال دیگری که میتوانم بزنم خودکفایی در طراحی و ساخت قالب است. الان توانایی طراحی و ساخت برخی از قالبهای مورد نیاز خود را در داخل کشور داریم. در خصوص تجهیزات آزمون و فیکسچرهای کنترلی نیز به همین ترتیب. در حال حاضر شرکتهایی هستند که میتوانند بسازند و تایید امور مهندسی متد ما را هم بگیرند.
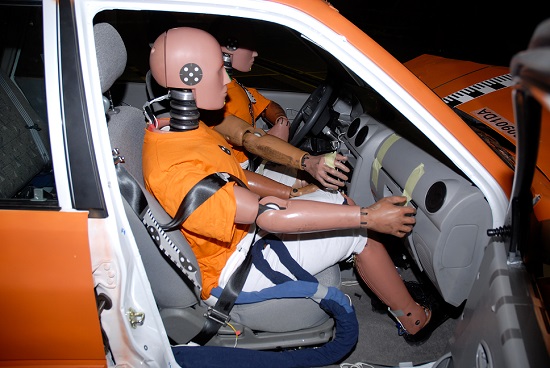 |
آزمون شبیهساز تصادف (crash) برای خودرو X100 در مرکز تست IDIADA |
یکی از اقدامات مهم در زمان تحریم که توسط سازندگان به انجام میرسید جایگزینی مواد یا ادوات ایرانی به جای موارد مشابه اروپایی است. آیا واحدهای مهندسی اثرات این تغییر مواد یا تجهیزات را مورد بررسی قرار میدهد و تاثیر آنها بر صحت انجام آزمونها و کیفیت محصولات را در نظر میگیرد؟
جایگزینی مواد، تنها به علت تحریم نیست. بسیاری از جایگزینیها مربوط به بومیسازی دانش و فناوری میشود. مثلاً فرض کنید شرکتی در کره جنوبی از ماده خاصی در محصولاتش استفاده میکند، نه صرفاً به علت ویژگیهای ماده، بلکه به علت در دسترس بودن، از آن استفاده کرده است. یکی از وظایف و نقشهای مهندسان این است که مشخصات مواد جدید که قرار است جایگزین شوند به دقت مورد ارزیابی قرار داده، تاثیرات آن را در ویژگیهای عملکردی و عمر محصول تعیین نمایند. طبیعتاً پس از هرگونه تغییری، نقشههای فنی و حتی آزمونهای قطعات تغییر میکنند. با این رویکرد به سمت موادی و قطعاتی رفتیم که قابلیت تامین آن ها در کشور و در منطقه خودمان بیشتر باشد. گاهی استفاده از مواد خاص در انواع مختلف فلزی یا پلیمری الزامی بود و باید مشابه آن را تولید میکردیم. بنابراین رفتیم به سمت اینکه تولیدکننده را فعال کنیم که بتواند مواد مورد نظر ما را تولید کند. فولاد مبارکه را میتوان در گروه همین شرکتها قرار داد. این شرکت به دلیل اعلام نیاز و تمرکز ما بر روی مواد خاص مورد نیازمان توانست محصولات خود را تنوع بخشیده و ورقی که قبلاً در دامنه محصولاتش نبود؛ تولید نماید.
الان ورق ها را خودتان تأمین میکنید؟ میزان خودکفایی آن ها چه مقدار است؟
در تامین و جایگزینی ورقها و مواد پلیمری به نتایج خوبی رسیدهایم و توانستهایم بیشتر ورقهای مورد نیازمان را خودمان تامین کنیم. به دلیل این که تولید مقدار کم، صرفه اقتصادی ندارد. مصرفِ هریک از سازندگان و پیمانکاران ما پایین است. گاهی مصرف مجموع آن ها یک بچ را پوشش میدهد. بنابراین مواد را برای مدت طولانیتر باید بخریم و به تدریج مصرف کنیم. این کار را سازهگستر انجام میدهد. مدیریت ما در مهندسی محصول در جایگزینی ورقها توانسته است سایز، اندازه و مواد را بهینهسازی نماید. در تامین مواد پلیمری مورد نیاز واحدهای پتروشیمی را هم فعال کردهایم. ما در این جا دو نقش داشتهایم: اول مشخصات مواد را تعریف کردیم، و بعد به کنترل و صحهگذاری آن ها پرداختیم. در بحث خودکفایی در سه سال گذشته، کارهای زیادی انجام دادیم. در بعضی از محصولات تا حد هشتاد درصد کاهش مصرف مواد خارجی داشتیم. که همچنان به دنبال کاهش این میزان وابستگی هستیم.
در بحث خودکفایی در سه سال گذشته، کارهای زیادی انجام دادیم. در بعضی از محصولات تا حد هشتاد درصد کاهش مصرف مواد خارجی داشتیم. که همچنان به دنبال کاهش این میزان وابستگی هستیم.
در خصوص بومیسازی مواد آیا با سایر خودروسازها هماهنگ بودهاید؟
بله؛ مثلاً اگر قرار بود فولاد مبارکه فقط برای ما محصولی را تولیدکند شاید برایش صرفه اقتصادی نداشت. ولی الان با توجه به یکپارچگی و حجم درخواستها به جایی رسیده است که برای پاسخگویی نیاز به افزایش ظرفیت دارد.
عمدهترین فعالیتهای شرکت در بخش صادرات در حوزه های مهندسی، محصول و قطعه چه بوده است؟
صادرات در گروه سایپا همیشه یکی از موضوعات مهم و مورد توجه بوده است و همان طورکه میدانید در بخش صادرات موفقترین شرکت هستیم. واحد صادرات ما چه در خودروسازی و چه در سازهگستر بسیار فعال عمل میکند و تقریباً تمام محصولات جدیدمان با نگرش صادراتی تولید شدهاند. پروژههای آینده نیز با نگاه به صادرات تولید میشوند. پیادهسازی و رعایت بعضی از استانداردها فقط به لحاظ جنبههای صادراتی محصول است. از همان ابتدا با نگاه به صادرات طراحی و مشخصه های فنی قطعات را تحت کنترل داریم. مشتریان ما به تبع همان تغییراتی که در سطح جهان رخ داده و به کمک ارتباط با کشورها و خودروسازهای دیگر روز به روز خواستههایشان را سنگینتر و سختتر میکنند و الزامات خود را ارتقا میدهند. بنابراین ما هم مجبوریم خودمان را تطبیق دهیم.
همان طور که مطلع هستید آلودگی هوا بخصوص در فصل زمستان مشکلات بزرگی را برای مردم ایجاد میکند. فعالیتهایی که در واحد مهندسی برای حل این معضل انجام شده است تا این معضل هم در خودروهای قدیمی و هم در خودروهای جدید، کمتر شود، چه بوده است؟
به دلیل اینکه بخش عمدهای از مباحث آلایندگی خودرو به عملکرد موتور برمیگردد و با توجه به تولید موتور (Power train) که عمدتاً در شرکت مگاموتور انجام میشود؛ عملاً ما نقش چندانی در این خصوص نداریم. مگر در اجزای جانبی موتور یا سیستمهای نگهداری و انتقال سوخت که در تمامی این حوزهها کار کردهایم و اثربخش بودهایم. به عنوان مثال در سیستم سوخت رسانی مساله نشت بخارات مهمترین عامل آلایندگی است؛ لذا تلاش کردیم مشکل را برطرف کنیم.
در حالت کلی در مواردی که خودروساز استانداردهای کاری خود را عوض کرده یا ارتقا داده است، ما هم خودمان را تطبیق دادهایم. در حال حاضر استاندارد یورو چهار (Euro 4) رواج دارد. در تمامی مراحل طراحی و تکوین، محصولات خود را متناسب با آن طراحی و تطبیق دادهایم. ما اثرگذار هستیم ولی تعریف کننده نیستیم. اما در بعضی موارد چارهای نداریم؛ مثلاً در فرمان هیدرولیک به دلیل استفاده از مواد پلیمری و احتمال نشت بخارات که خود یک عامل آلایندگی است؛ برای حل این مشکل بر روی فرمان برقی تمرکز کردهایم؛ که از دو بعد مفید است، یکی حذف مواد هیدرولیکی و دیگری کاهش مصرف سوخت به دلیل کاهش توان موتوری.
تمام مباحثی که در اینجا فرمودید، در شرکت ایرانخودرو یا سایر خودروسازان داخلی نیز به نحوی مطرح است. چقدر با سایر خودروسازان که دغدغههای مشابهی دارند، ارتباط دارید؟ با توجه به آنکه نداشتن ارتباط، در بخشهایی ممکن است مشکلاتی به وجود آورد؛ مثلاً در بخش مهندسی متد، یک دستگاه تست توسط نماینده یک خودروساز طراحی و مورد تایید قرار میگیرد و نماینده خودروساز دیگر دستگاه دیگری را تایید میکند. از منظر عمومی نباید سوء برداشت شود مبنی برآنکه خودروسازها کارهای متفاوتی انجام میدهند. نظر شما در این باره چیست؟
از کار مشترک، همافزایی به وجود خواهد آمد که همواره مثبت است. ضمن اینکه ما خود را با شرکتهای دیگر رقیب نمیدانیم، هر توسعه و رشد پایداری که در حوزههای مهندسی و کیفیت در زنجیره تأمین یا خودروساز اتفاق میافتد، به دلیل اشتراکاتی است که در زنجیرههای تامین و خودروسازان وجود داشته است. در سطح دو گروه سایپا و ایران خودرو همیشه این ارتباط وجود دارد. فرد به فرد و سازمان به سازمان این همکاری ها را شاهد هستیم؛ در عین حال بعضی از اطلاعات قابل انتقال نیست و مختص هر پروژه و خود مجموعه است. در شرکت سازهگستر مقایسه بازار و شبیهسازی پروژهها (benchmark) به خوبی در واحد مهندسی انجام میشود. برای این منظور یک کارگاه نسبتاً کامل وجود دارد که همواره فعالیتهای شبیهسازی و (benchmark) آن به طور کامل مدون و روتین شده است.
در این کارگاه بر روی مجموعه خودرو، قطعات و فرایندها به صورت مستقل و مستمر موضوعات تعریف شده و مطابق با برنامههای تدوین شده کار میشود. نهایتاً با تثبیت نتایج و نهادینه شدن خروجیها متناسب با موضوعات مطرح شده دانش هر بخش کسب میشود.
فعالیت معاونت مهندسی سازهگستر در دو راستای کاهش هزینه و ارتقای کیفیت قطعات چه بوده است؟
تولید از دو بُعد مهندسی و کیفیت قابل بررسی است. هدف واحد کیفیت، کنترل و نظارت تولید، مطابق با خواسته مشتریان است. ولی در بخش مهندسی تمرکز بر تغییرات برای رسیدن به کیفیت است؛ یعنی واحدهای کیفی نظارت میکنند که مطابق با تعریف اولیه و استاندارد شده تولید صورت پذیرد. اما واحد مهندسی با تعریف و اعمال تغییرات سعی در تولید محصول باکیفیتتر میکند. با همکاری این دو واحد اثر تغییرات، خود را در بهبود کیفیت محصول و کاهش هزینهها نمایان میکند.
ما در معاونت مهندسی سالانه چیزی حدود پنجاه پروژه تعریف میکنیم. بخشی از این پروژهها کیفی است. بخشی دیگر مربوط به کنترل و کاهش هزینهها و برخی دیگر مربوط به سهولت انجام کار و بهینهسازی فرآیندهای تولیدی است.
با وجود این حجم پروژههای تعریف شده، دستاورد بزرگی که امور مهندسی سازهگستر داشته چه بوده است؟
اولین دستاورد ما مدیریت زنجیره تامین مطابق با چارچوب و تعاریف سازمانی است. بدون زنجیره تامین ما هم وجود نداریم. به عبارت دیگر بهبود کیفیت، تغییرات مهندسی محصول یا کاهش قیمت تمام شده صرفاً با حضور سازندگان امکانپذیر است. بدون کمک سازنده و حضورش در تیمهای تعریف شده؛ عملاً کاری انجام نمیشود. در سالهای گذشته، دستاوردهای بزرگی در کاهش قیمت تمام شده محصول از طریق تغییرات مهندسی و بهبود فرآیند تولید و مواد اولیه داشتهایم که همه اینها با حضور و کمک سازندگان امکانپذیر بوده است.
کار بزرگی که امسال آغاز کردیم، تشکیل زنجیره مهندسی تحقیق و توسعه (R&D) سازندگان است. یعنی با فرض اینکه هر سازندهای دارای واحد مستقل مهندسی تحقیق و توسعه است و مجموعه توانمندی و قابلیتهای باارزشی را در حوزه مرتبط با خود فراهم کرده است که شناخته شده نیز نیست؛ سعی کردیم با برقراری ارتباط بین دو واحد مهندسی تحقیق و توسعه خودمان و آن واحد تولیدی به این فعالیتها انسجام بخشیده و اثربخش بودن این روش را به آنها نشان دهیم. یکی از نشانههای اثربخشی در ارتباط با خودروساز همجوار خود است که با ارتقای دانش و سطح توانمندیهای زنجیره تامین در مهندسی R&D این قابلیت به صورت منسجم قابل بهرهبرداری در بخشهای دیگر صنعتی خواهد بود. اتفاق خوب دیگری که میافتد آن است که هرگونه بهبودی که در شبکه تامینکنندگان ایجاد میشود به دلیل وجود زنجیره اطلاعاتی که از طریق ما در مهندسی R&D شکل گرفته است قابل تعمیم و انتشار به سایر اعضای شبکه است و اطلاعاتی که میتواند برطرف کننده مشکلات عدیده تولید یا کیفیت محصولات باشد مغفول نمیماند. در واقع همیشه در سالهای گذشته یکی از مشکلاتمان این بود که سازندهای کاری میکرد و فرایندش را بهبود میداد، ولی سازنده دیگر اطلاعی از آن نداشت چون با هم ارتباطی نداشتند. ما ارتباط بین سازندهها را برقرار کردیم و به این شیوه یادگیری و هم افزایی داشتیم.
در سالهای گذشته، دستاوردهای بزرگی در کاهش قیمت تمام شده محصول از طریق تغییرات مهندسی و بهبود فرآیند تولید و مواد اولیه داشتهایم که همه اینها با حضور و کمک سازندگان امکانپذیر بوده است.
ممکن است مقاومت هم از طرف رقبا وجود داشته باشد. بسیاری از طراحان وتولیدکنندگان تمایلی ندارند که مالکیت معنوی طرح خود را با دیگران تقسیم کنند.
تاکنون اصلاً شاهد چنین مقاومتی نبودهایم. اتفاقاً یکی از زمینههایی که در آن رشد کردهایم، همین است. سازندهای دیدم که میگوید من دانش خودم را در اختیار هرکسی که بتواند جذب کند قرار میدهم. یکی از دستاوردهای مهم صنعت خودرو، به وجود آوردن چنین زنجیرههایی است. صنعت خودرو در بسیاری از زمینهها پیشتاز بوده است به نحوی که بسیاری از صنایع دیگر به آن وابسته هستند.
سپاس گزاریم از این که وقت خود را در اختیار ما گذاشتید.