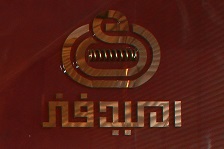
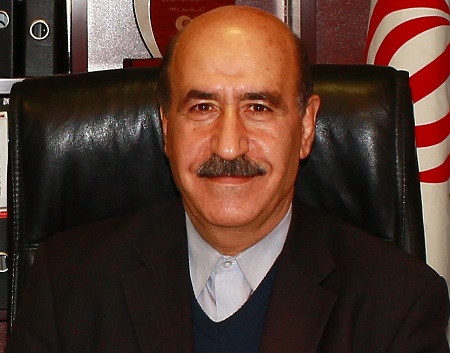
گروه صنعتی امید فنر
اندیشهای پویا
پیشینهای کهن
غلامرضا محمدیپور؛
بنیانگذار صنعت فنر نوین در ایران
ظهور یک صنعت و تکنولوژیِ جدید، نیازمند پیشرو و پیشگام است. در گروه "اولینها" بودن، همیشه سخت و جانفرساست. پیشگام بودن، ارادهای قدرتمند و استقامتی دوچندان میخواهد. پای صحبتهای پیشگامان صنعت که بنشینی، باور به خواستن و توانستن، ایمان به غیرت ملی، تکیه بر دانش بومی و ترسیم آیندهای شکوهمند موج میزند. مردانی از جنس فولاد که از پس سختترین روزها هم با قدرت فولادین برآمدند ...
بومیسازی صنعت فنر و تولید ملی آن در کشور در سال 1353 با همت و تلاش جناب آقای غلامرضا محمدیپور شکل گرفت. اولین فنرساز ایران که در برخی محافل با عنوان "پدر فنر ایران" شناخته میشود؛ کار خود را در یک کارگاه سنتی آغاز کرده و در سال 1362 موفق به تأسیس گروه صنعتی امیدفنر گردید. با این کار صنعت فنرسازی در ایران به صورت جدی متولد شد و تولید فنر از حالت سنتی به تولید صنعتی رسید. همت و تجربه بالای مدیران شرکت و بهرهمندی از متخصصین دانشمند و متعهد، شرکت امیدفنر را پس از 30 سال فعالیت به عنوان منبع اصلی تأمین انواع فنرهای صنعتی در کشور مطرح نموده است. این شرکت با بهرهگیری از بهروزترین دستگاههای تولید فنر و با داشتن آزمایشگاهی مجهز و پشتوانهای مطمئن از مواد اولیه، تأمین طیف متنوعی از فنرها را به لحاظ شکل، جنس و سایز مفتول (از جمله انواع فنرهای فشاری، پیچشی، کششی و فرمینگ) عهدهدار است. در حال حاضر شرکت صنعتی امیدفنر تأمینکننده اصلی خطوط تولید کلیه خودروسازان کشور بوده و بیشترین سهم بازار قطعات یدکی را نیز به خود اختصاص داده است. به علاوه این شرکت در تأمین سایر بازارها از جمله صنایع نفت و گاز، صنایع ریلی، صنایع هوایی، صنایع کشاورزی، لوازم خانگی، برق و ساختمان، مبلمان اداری و ... نیز فعالیت عمدهای دارد. در حال حاضر شرکت صنعتی امیدفنر قدیمیترین عضو گروه صنعتی امید است که از دیگر اعضای این گروه میتوان شرکتهای آلیاژ فنر امید و امید فولاد هیراد اشاره نمود.
گزیدهای از افتخارات:
-
1394: کسب عنوان کارآفرین برتر در سیزدهمین جشنواره تولید ملی افتخار ملی از سوی ریاست خانه صنعت معدن و تجارت
-
1394: کسب عنوان واحد نمونه صنعتی استان قم
-
1393: کسب عنوان کارآفرین نمونه استان قم
-
1392: اخذ گرید A از شرکت ساپکو ( مهندسی و تأمین قطعات ایران خودرو)
-
1389: اخذ استاندارد BS OHSAS 18001:2007
-
1389: اخذ استاندارد ISO 14001:2009
-
1390: اخذ گرید A شرکت سازهگستر سایپا (مهندسی و تأمین قطعات سایپا)
-
1389: اخذ استاندارد ISO IEC 17025:2005
-
1389: کسب عنوان قطعهساز برتر در زنجیره تأمین ساپکو (مهندسی و تأمین قطعات ایرانخودرو)
-
دریافت تندیس افتخار در ششمین همایش بینالمللی موتورهای درونسوز (به عنوان قطعهساز برتر)
-
اخذ استاندارد ISO/TS 16949:2009
-
اخذ استاندارد ISO 9001:2008
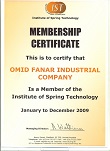
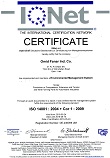
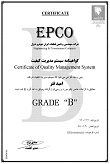
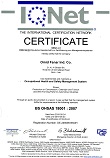
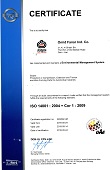
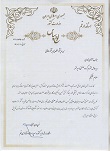
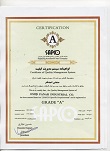
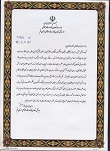
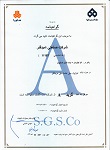
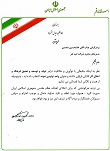
جناب آقای مهندس غلامرضا محمدیپور مدیریت محترم گروه صنعتی امیدفنر ضمن تشکر از وقتی که در اختیار "نشریه فناوری آزمون و اندازه گیری" قرار داده اید، لطفاً از سالهای اولیه و شروع کار خود بفرمایید.
غلامرضا محمدیپور هستم؛ بنیانگذار صنعت فنر یا به عبارتی صنعت فنر نوین در ایران. ایده اولیه برای شروع به فعالیت در این حوزه در 1352، وقتی با فردی به نام آقای بخانیان آشنا شدم، در ذهن من شکل گرفت. وی در آن زمان در کارگاه کوچکی فنر مبل و فنر صندلی پیکان را تولید میکرد. به خود گفتم: "چرا من نتوانم؟" و اینگونه شد که فعالیت ما از سال 1353 در یک کارگاه کوچک به صورت سنتی آغاز گردید. دستگاههایی را از شرکت شنکر سوییس خریدیم و در مقیاس محدود شروع به تولید کردیم. در سال 1358 با نظر به فرمان امام خمینی(ره) تصمیم گرفتیم کار را توسعه داده و فنرسازی سنتی را وارد گردانه فنر صنعتی کنیم. به این منظور به وزارت صنایع مراجعه و توانستیم موافقت اصولی آن زمان را اخذ کنیم. اوایل سال 1361 مراحل مقدماتی انجام کار صورت گرفت. برای کسب موافقت اصولی محدودیتهایی وجود داشت از جمله برای احداث واحد تولیدی باید تا شعاع 120 کیلومتری از تهران خارج میشدیم. برای این منظور شهر قم یعنی زادگاهم را انتخاب کردم. در ابتدا به من اجازه تأسیس واحد صنعتی در قم را ندادند. گفتند شهر قم شهری مذهبی است و نباید به یک شهر صنعتی تبدیل شود. ولی با پیگیریهای زیاد توانستیم نخستین واحد کارخانهای خود را در قم تأسیس کنیم. بدینگونه فعالیت حرفهای گروه صنعتی فنر آغاز شد. به این ترتیب که سال ۱۳۶۱ موافقت را اخذ و ۴ سال بعد یعنی سال ۱۳۶۵ در زمینی به مساحت ۶ هزار متر مربع و در دو سوله کار را آغاز کردیم. به لطف خداوند متعال و با همت تمامی اعضای این گروه، تا به امروز توانستهایم موفقیتهای زیادی کسب کنیم. در حال حاضر نه تنها با سابقهترین، بزرگترین و پایدارترین شرکت در صنعت فنرسازی در ایران هستیم؛ بلکه توانستهایم در این حوزه در منطقه هم پیشتاز باشیم.
شروع برنامههای توسعهای گروه صنعتی امیدفنر برای پایهگذاری شرکتهای آلیاژ فنر امید و امیدفولاد هیراد از چه سالی و با چه هدفی صورت گرفت؟
صنعت فنر، دامنه وسیعی دارد و در اکثر صنایع از جمله خودروسازی، موتورسیکلتسازی، مبلمان و لوازم منزل کاربرد دارد. ما به خوبی این را میدانستیم و متوجه شدیم که امیدفنر در حوزه فعالیتهای خود به اندازه کافی و مورد نیاز توسعه پیدا کرده است. اما در بخش تولید مواد اولیه، در ایران اقدامی صورت نگرفته بود. به عبارتی دیگر بعد از گذشت چند دهه از انقلاب اسلامی هنوز مواد اولیه از خارج وارد میشد. تجربیات، سوابق و دانش ما در این حوزه پاسخگوی این نیاز بود. بنابراین با هدف فراهم آوردن مواد اولیه مورد نیاز، تصمیم به توسعه گرفتیم.
بدین ترتیب پروژه تاسیس عضو دیگری از گروه صنعتی امیدفنر از سال 1389 با تخصیص بودجهای کلان و با هدف خودکفایی با نام " آلیاژ فنر امید" در دستور کار قرار گرفت. آلیاژ فنر، وظیفه تولید آلیاژها و مواد اولیه را دارد که در تولید فنر مورد نیاز است. پس از پایهگذاری شرکت آلیاژفنر امید برای داشتن پشتوانهای قویتر در فراهم کردن مواد اولیه، شرکت "امیدفولاد هیراد" تاسیس شد. برای اینکه بتوانیم همواره با قدرت تمام در بازار حاضر باشیم باید دغدغه تأمین مواد اولیه را در هیچ شرایطی نداشته باشیم. برخی از مواد اولیه وجود دارد که در حال حاضر تکنولوژی داخلی کشور، توان تولید آن را ندارد. فراهم کردن این مواد بر عهده شرکت امیدفولاد هیراد است. رسالت هیراد، انجام فعالیتهای تجاری است. این شرکت به عنوان عضو ی از اعضای گروه صنعتی امیدفنر، یاریگر آلیاژفنر در فراهم کردن مواد اولیه است و در پخش محصول به امیدفنر کمک میکند.
مهمترین صنایعی که در زنجیره مشتریان شما قرار میگیرند؛ کدامند؟
متأسفانه در شرایط فعلی مجموعههای غیراستاندارد بسیاری در این حوزه در کشور وجود دارند که بدون رعایت اصول اولیه و نظارت کیفی مناسب فعالیت میکنند. تولیدات این مجموعهها آزمونهای لازم و استانداردهای مورد نیاز را پشت سر نگذاشتهاند. برای اینکه بتوانیم تمایز خود را مشخص کنیم همواره به دنبال صنایعی بودیم که با جدیت و دقت الزامات استانداردها، آزمون و کیفیت را دنبال میکنند. از جمله این صنایع، صنایع خودروسازی هستند. ما تصمیم گرفتیم بیشتر تولیدات خود را به سمت خودروسازان سوق دهیم. زیرا رعایت اصول استاندارد در خودروسازی به عنوان یک الزام همواره مطرح بوده است. با این برنامهریزی، بیشتر ظرفیت خود یعنی در حدود ۷۵ درصد را برای صنایع خودروسازی ایران، قطعه سازان و مجموعهسازها اختصاص دادهایم و قسمتی از آن نیز متعلق به بخش مبلمان اداری و لوازم منزل است. البته با صنایع هواپیمایی و ریلی نیز همکاری میکنیم؛ اما تمرکز اصلی ما روی خودروسازیهاست. از حدود 10 سال پیش؛ ما و چند شرکت دیگر، تولید فنر مورد نیاز صنعت خودرو را بر عهده داشتهایم. اما از سال 1391 برخی فنرسازها به خاطر چالشهای موجود همکاری با صنایع خودروسازی را کنار گذاشتند. در حال حاضر، شرکت امیدفنر 80 درصد فنر مورد نیاز دو خودروسازی کشور را تأمین میکند.
در حال حاضر در گروه صنعتی امید فنر محصولات مهمی از جمله فنر سوپاپ و ترمز به صورت تخصصی تولید میشوند که از تکنولوژی و دانش بالایی برخوردار بوده و ساخت چنین قطعاتی با ضریب ایمنی بالا بسیار ارزشمند و نیازمند تکنولوژی بالاست. شرایط تولید این محصول و نحوه کسب فناوری مورد نظر را بفرمایید؟
مواد اولیه، تولید و آزمون فنر سوپاپ شرایط بسیار خاصی دارد. در حال حاضر ما بیش از 70 درصد فنر سوپاپ مورد نیاز ایرانخودرو و ساپکو، سایپا و سازهگستر را تأمین میکنیم. ساخت این فنرها به تجهیزات و دانش خاصی نیازمند است. بخشی از این دانش را وارد کردیم و بخشی را در واحد خودمان و توسط متخصصین ایرانی توسعه دادیم. علاوه بر این موضوع، محصول دیگری اخیرا و با ریسک سرمایه گذاری بالا اقدام به راه اندازی خط تولید آن کرده ایم فنر رینگ روغن موتور خودرو بوده است . خودرو بود. این نوع فنر، هنوز هم از کشور ترکیه وارد میشود و در ایران تولید نمیشود. که عمدتا دو دلیل دارد : اول اینکه خط تولید و تجهیزات خاص تولیدی و کنترلی نیاز دارد ، دوم اینکه زیرا مشتری خاص دارد در نتیجه از نظر تجاری کسی ریسک این کار را نمی پذیرد. اما امیدفنر، این را ریسک را پذیرفته و در حال حاضر نمونههای اولیه این فنر جهت انجام آزمونهای نهایی تحویل شرکت ساپکو شده است در واقع ما نخستین شرکت ایرانی هستیم که تکنولوژی تولید فنر رینگ روغن موتور خودرو را دارا می باشد .
از نظر یک صنعتگر ایرانی اصلاً پسندیده نخواهد بود که بعد از گذشت ۳۰ سال تجربه، همچنان این فنر از ترکیه وارد کشور شود. به همین خاطر ریسک سرمایهگذاری آن را پذیرفته و دست به تولید آن زدیم. این فنر بسیار ظریف و قطر خارجی آن در حد ۲ میلیمتر است. مواد تشکیلدهنده این فنر هم از فولاد خاص و از خانواده کرم سیلیکون است که طی یک فرایند پیچیده تولید میگردد. طی کردن این پروسه نیاز به دانش خاصی دارد و مواد اولیه آن نیز در حال حاضر از خارج از کشور فراهم میشود.
محصول جدید دیگری که در سال 1395 خط تولید آن راه اندازی و به مرحله تولید انبوه رسید فنر کمربند ایمنی خودرو بود . شرکت امید فنر تحت لیسانس یک شرکت مطرح کره ای در کلاس جهانی و با سرمایه گذاری بالا موفق شد به تکنولوژی تولید این فنر دست یافته و آنرا به تولید انبوه برساند .
نقطه قوت و دلیل اصلی موفقیت گروه صنعتی امیدفنر را در چه میدانید؟
نقاط قوت گروه صنعتی امید در چندین حوزه قابل بررسی است:
اول اینکه ما همیشه تجهیزات مناسب و ایدهآل داشتهایم. سعی کردهایم همگام با پیشرفت جهان، تجهیزات و فناوری خود را توسعه دهیم.
دومین عامل موفقیت شرکت، مدیریت خانوادگی مجموعه است. ما همواره بهصورت خانوادگی شرکت را اداره کردهایم. اینگونه شد که وحدت مدیریتی مجموعه به بیشینه خود رسید. اما مهمترین عامل موفقیت برای ما اهمیت و ارزشمندی بحث کیفیت در گروه صنعتی امیدفنر بود. ما هیچگاه از استاندارهایی که مرسوم بوده است، غافل نشده و همیشه بهروز بودهایم. چندین دهه تجربه به من آموخته است که باید برای دانش و تخصص نوین دنیا، سرمایهگذاری کرد. همواره استانداردهای روز دنیا را پیگیری کرده و به دنبال کسب آن بودیم. از جمله این استانداردها ISO/TS، ISO14000 و ISO9000 بوده و واحد آزمایشگاه شرکت، استاندارد 17025 را داراست. یکی از مهمترین عللی که باعث شده نسبت به رقبایمان متمایز باشیم، این بوده است که همیشه بهروز بودیم و مدیریت مجموعه این تمایل را داشته است که در حوزه دانش و تکنولوژی سرمایهگذاری کند. بدین معنی که طرح توسعه ما از داخل مجموعه شکل گرفته است.
شما به این نکته اشاره کردید که شرکت امیدفنر توانسته است در بازار داخلی ماشینآلات تولیدی و تجهیزات بهروزی داشته باشد. با توجه به تحریمها چگونه تجهیزات مورد نیاز خود را از طریق بازارهای خارجی تأمین میکردید؟
در صنعت فنر معمولاً طرحهای توسعهای و جدید براساس سفارشات خاصی صورت میگیرد. هر زمان مجموعه تصمیم بر تولید فنر جدیدی بگیرد یا مشتری سفارش فنر خاصی را به شرکت ارائه دهد، واحد تحقیق و توسعه و دفتر مهندسی شرکت این پروژه را بررسی میکند. مشتری برای ساخت این تجهیزات، نمونه یا نقشه درخواستی خود را ارائه میدهد. یا اینکه طرحی ندارد اما یکسری درخواستهایی دارد. در این صورت، واحد تحقیق و توسعه شرکت امیدفنر با بررسیهای لازم و اخذ مجموعه اطلاعات، محاسبات لازم را انجام داده و مدل اولیه را طراحی و شبیهسازی میکند. در نهایت با رعایت استانداردهای جهانی طراحی فنر و نرم افزارهای بهروز مدل نهایی فنر طراحی میشود. پس از مرحله طراحی و ساخت، در مرحله کنترل کیفیت فنر از لحاظ کلیه موارد، تحت بررسی قرار میگیرد. مثلاً به این نتیجه میرسیم که در حوزه پیچش فنر مشکلی نیست اما در حوزه تنشزدایی مشکل وجود دارد. اگر آزمونهای موجود جواب داد که به نتیجه رسیدهایم؛ اما اگر جواب نداد شرایط مناسب و تجهیزات لازم برای آزمون مورد نظر را تهیه میکنیم. میزان اهمیت آزمون، کیفیت و دقت از نکات تاثیرگذار در انتخاب تجهیزات آزمون است. کیفیت برای ما همیشه حرف اول را میزند. اولویت ما حمایت از سازندگان ایرانی بوده و هست، اما باید اطمینان حاصل کنیم که کیفیت مورد نیاز ما را تأمین میکند. اما اگر نتوانیم از منابع ایرانی کیفیت مورد نظر را فراهم کنیم، به ناچار از منابع خارجی کمک میگیریم. انتخاب ما در این مورد بدون شک، شرکتهای معتبر اروپایی هستند. زیرا کیفیت و دقت بسیار بالایی دارند و به ما اطمینان خاطر میدهند. فنر قطعه بسیار حساسی است و بحث کنترل کیفی آن بسیار حائز اهمیت است. این اطمینان موجب شده حتی با تمام مشکلاتی که در فراهم کردن آنهاوجود دارد، اولویت اصلی ما تهیه تجهیزات باشد.
به عنوان مثال در بخش تولید در شرکت آلیاژ فنر نیاز به دستگاه آزمون غیر مخرب جریان گردابی (Eddy Current) داشتیم. اهمیت بسیار بالای این آزمون موجب شد که این دستگاه را از یک شرکت آلمانی و دقیقترین نوع آن را با قیمت بسیار بالا فراهم کنیم که بالاترین تکنولوژی را در این حوزه دارد.
برای حضور در بازار خارجی و انجام صادرات برنامههایی داشتهاید؟
تمامی شاخصهایی که برای صادرات محصول مورد نیاز بوده، بررسی شده است. مخصوصاً چون محصولات ما حجیم نیستند، شرایط مناسبی برای صادرات دارند. لازمه صادرات این است که با شرکتها و کشورهای مطرح دنیا در تعامل باشیم.
زمانی هندیها اعلام کردند که میخواهند محصول آلیاژ فنر را از شرکت ما خریداری کنند. اقدامات لازم را انجام دادیم و با هزینه خود محصول را برای آنها ارسال کردیم. آنها مفتول را پیچیدند و تأیید کردند و از کیفیت کار بسیار راضی بودند. ما هم برای اینکه در بستر صادرات قرار بگیریم؛ در موارد مالی، شرایط آنها را پذیرفتیم. بعد از این سفارش، از آنها خبری نشد. اخیراً واحد توسعه اعلام کرده است که شرکت مذکور سفارش ساخت نمونه بعدی خود را به ترکیه داده است. فنر تولیدی ما از نظر کنترل کیفیت، محاسبات و سایر فاکتورهای فنی بسیار ایدهآل است. تجربه مشابه دیگری هم در بحث صادرات با کشور ترکیه داشتیم. برای همکاری با یکی از معتبرترین شرکتهای کلاچ سازی ترکیه در مزایدهای برای تأمین فنرهای کلاچ خودرو، شرکت کردیم. در آنجا هم به توافق رسیدیم. از مجموعه بازدید و تمام دستگاهها را تأیید کردند. فقط خواستند یک دستگاه خاصی را هم فراهم کنیم. ما این کار را هم کردیم؛ اما دیگر به ما مراجعه نکردند. به نظرم این موضوع بُعد فنی ندارد بلکه آنها تمایلی به خرید از ما به عنوان یک شرکت ایرانی ندارند.
متأسفانه نه تنها در بحث صادرات چالشهایی وجود دارد بلکه اگر جدیت به خرج ندهیم بازار خدمات پس از فروش داخلی را هم از دست میدهیم. با توجه به هجوم قطعات هندی و چینی متأسفانه حدود 75 درصد بازار خدمات پس از فروش در دست آنهاست. باید برای این بازار فکری کرد. سهم صنایع خودروسازی و قطعهسازی ایرانی از این بازار، فقط 25 درصد است. به این موضوع نسبت به بحث صادرات اهمیتی دوچندان میدهیم.
فکر می کنید چرا تا به این میزان، بازار خدمات پس از فروش ایران از اجناس و کالاهای چینی و هندی اشباع شده است؟
میزان حمایت از تولیدکننده داخلی کم شده است. به طور مثال بانکها برای ما به عنوان تولیدکننده داخلی کارمزد را حدود 20 درصد تعیین میکنند ولی بانکهای چینی تسهیلات را با سود حدود 5 درصد در اختیار تولید کننده چینی قرار می دهند. در مقایسه با کشورهای دیگر هیچ حمایت خاصی از تولیدکننده داخلی انجام نمیشود. ما اگر قصد توسعه داشته باشیم باید زمین را با قیمت متر مربعی 33 دلار بخریم اما در شانگهای چین زمین تقریبا رایگان به تولیدکننده داده میشود. بنابراین مجبوریم از بانکها وامهایی با بهرههای بالا بگیریم و این یعنی عدم امنیت در تأمین منابع مالی که خواسته یا ناخواسته بر قیمت تمام شده محصولات ما اثرگذار خواهد بود.
به عنوان یک صنعتگر موفق با گذشت سالها تجربه بزرگترین مشکلات و چالشهای تولیدکنندگان داخلی را چه میدانید؟
موضوعی که موجب آزار ما میشود عدم نظارت کافی بر کارگاههای صنعتی و تولیدی است. به کرّات دیده شده است که یکی از مجموعهسازها فنر شرکت ما را خریداری کرده و بعد از گرفتن تأییدیه، زمانی که میخواهد به تولید انبوه برساند، محصول خود را به کارگاههای غیر استاندارد میدهد تا آن را تولید کنند. کارگاههایی که هیچ نظارتی بر آنها نبوده و هیچ مرز و قاعدهای ندارند. شاید در شرایط فعلی بتوان این موضع را نادیده گرفت اما در آیندهای بسیار نزدیک تنها قطعهسازانی در صنعت پایدار و باقی خواهند ماند که تولیدات آنها مطابق با بهروزترین استانداردهای جهانی باشد.
چالش بعدی مسائل مالی و بحث نقدینگی است. نقدینگی حرف اول را میزند. پرداخت حقوق و تأمین هزینه تشکیلات و مواد اولیه موضوع مهمی است. چرخش طولانی کار موجب مشکلات مالی میشود. با توجه به مشکلات فراوان نقدینگی ایجاد یک تعادل نسبی در مجموعه کار بسیار دشواری است. نکته دیگری هم که در بخش توسعه و در زمان راهاندازی کارخانه آلیاژ فنر با آن روبهرو شدیم، تفاوت نوع نگاه به تولیدکننده ایرانی و خارجی است. کارشناسان و بازرسان کنترل کیفیت در مورد تولیدکنندگان داخلی سختگیرانهتر عمل میکنند و در مقابل سازندگان خارجی با انعطاف بیشتر رفتار میکنند. تولیدکننده داخلی از رعایت الزامات کیفی هیچ ابایی ندارد و از آن استقبال هم میکند اما لازمه آن این است که نوع نگاه کیفی در برابر همه یکسان و سختگیرانه باشد.
به عنوان یک پیشکسوت، نقش فناوری آزمون و اندازهگیری در ارتقای صنعت فنر را به چه میزان پراهمیت میدانید؟
سوال شما را با یک مثال پاسخ میدهم. بعد از دولت آقای هاشمی رفسنجانی تغییرات ناگهانی در صنعت و اقتصاد ایجاد شد. تنها شرکتهایی توانستند از تغییرات ایجاد شده موفق عبور کنند که زیرساختهای فنی و نیروی متخصص مورد نیاز را فراهم کرده بودند. شرکتهایی که تجهیزات مناسب و با کیفیت در کنار دانش فنی لازم را داشتند. ما قبل از دلار 400 تومانی هم یک فنرساز بودیم و حالا نیز یک فنرساز هستیم. چون همواره به زیرساختهای فنی و مهندسی، تجهیزات آزمون، مهندسی تحقیقات و توسعه و کنترل کیفیت بسیار اهمیت میدهیم. بر این باورم که تولید کیفی ماندگاری دارد و برای این ماندگاری، تولیدکننده باید عاشق کیفیت خوب باشد. ما در سال 1990 میلادی با شرکت شنکر سوییس کار میکردیم. با آنها تبادلات علمی و فنی داشتیم. هنوز هم بعد از 30 سال کار و تجربه، به دنبال این هستیم که با بزرگترین فنرسازان دنیا همکار شویم تا از جدیدترین تکنولوژی صنعت فنر استفاده کنیم.
تاکنون بالغ بر 3 میلیارد تومان در بخش آزمایشگاهی سرمایهگذاری کردهایم. چون فنر قطعهای بسیار دقیق و حساس است. دستگاهها و تجهیزات آزمایشگاهی را از منابع معتبر داخلی و برندهای مطرح جهانی تهیه میکنیم.
بنابراین بحث کنترل کیفیت برای شما و مجموعه بسیار حائز اهمیت است. در بخش آزمایشگاهها چه میزان سرمایهگذاری صورت گرفته است؟
تاکنون بالغ بر 3 میلیارد تومان در بخش آزمایشگاهی سرمایهگذاری کردهایم. چون فنر قطعهای بسیار دقیق و حساس است. دستگاهها و تجهیزات آزمایشگاهی را از منابع معتبر داخلی و برندهای مطرح جهانی تهیه میکنیم. در بحث کنترل کیفیت، به تجهیزات آسیای جنوب شرقی اعتماد نداریم. در نتیجه تجهیزات خود را از تولیدکنندگان داخلی یا برندهای مطرح اروپایی تأمین میکنیم. بنابراین هزینه تامین تجهیزات و میزان سرمایهگذاری در بخش آزمایشگاهی بسیار بالاست.
به عنوان مرجع آزمون فنر در کشور برنامهای برای توسعه آزمایشگاهی و تبدیل شدن به مرکز آزمون فنر دارید؟
بله؛ همکاری بسیار جدی و مهمی را با یکی از برندهای مطرح جهانی دنبال میکنیم. توافقات خوبی حاصل شده است. با حصول کامل به این توافقات، هر آزمونی که قیمت متوسطی داشته باشد و مهیا کردن آن برای آزمایشگاه میسر باشد، در داخل کشور فراهم خواهیم کرد و در مورد آزمونهای پرهزینه هم میتوانیم از خدمات آنها استفاده کنیم.
به چه علت به صورت مستقل آزمایشگاه را به عنوان مرجع آزمون مطرح نمیکنید و در کنار یک برند جهانی قرار میگیرید؟
شاید قرار گرفتن در کنار یک برند جهانی بهتر باشد. در حال حاضر افراد متخصص و باسابقه در حوزه فنرسازی از بزرگترین شرکتهای دنیا به صورت دورهای به شرکت ما مراجعه میکنند و حقیقتا نکات ظریف خاصی از این تعاملات عایدمان شده است.
یکی از موانع توسعه و پیشرفت در صنعت ما عدم وجود تجهیزات آزمون و اطلاعرسانی دقیق از آزمون صحیح است. به عنوان مثال اگر ما بخواهیم فرآیندی را نوآوری کنیم؛ برای صحهگذاری آن تجهیزات و استانداردهای مناسب نداریم. با توجه به هزینههای بالا اگر بخواهیم برای هر نوآوری و هر اقدام جدیدی تمام تجهیزات لازم را تهیه کنیم؛ امکانپذیر نیست. در چنین شرایطی فرد مجبور است بر اساس حدسیات و تجربیات خود تصمیم بگیرد. اینجاست که شما اگر در کنار یک برند مطرح جهانی باشید می توانید در موارد خاص از تجهیزات و تجربیات آنها هم استفاده و بهره برداری نمایید .
به عنوان پیشگام صنعت فنر، روند داخلی توسعه و گسترش صنعت فنرسازی را در داخل کشور چگونه ارزیابی میکنید؟
فنرسازی به دانش و تجربه نیاز دارد. شاید ظاهراً صنعت پیچیدهای نباشد، اما تنوع بسیار بالای محصولات و شرایط تولید و آزمون، مشقت زیادی دارد. صنعتگران دیگری نیز به این حوزه وارد شدهاند و این صنعت توسعه خوبی داشته است. اما با توجه به اینکه ما از قدمت 32 ساله برخوردار هستیم گروه صنعتی امیدفنر به یک الگو برای تولیدات داخلی فنر کشور تبدیل شده است.
اگر بخواهید نتیجه این چندین دهه تلاش و کوشش را در چند جمله بیان کنید، چه پیامی به مخاطبین ما خواهید داشت؟
تنها خواسته من از جامعه صنعتی کشور این است که تعصب ملی را بیشتر کنیم. قبل از نگاه اقتصادی و مالی نگاه ملی داشته باشیم. ما تا کی منتظر باشیم که قطعه، مفتول یا ماشین از خارج وارد شود؟ ما چه چیزی کمتر از بقیه داریم؟ چرا نتوانیم؟ در حال حاضر سالی یک میلیون خودرو تولید میکنیم و در میان کشورهایی قرار داریم که بیشترین میزان تولید خودرو را دارند. این موقعیت لذتبخش است اما اگر کیفیت داخلی نیز بیشتر شود، دوچندان لذت میبریم. ما باید عِرق ملی داشته باشیم و عاشق صنعت و کارآفرینی باشیم. در این صورت است که اقتصاد ملی شکل میگیرد. بسیار لذتبخش است که توانستیم مفتول را در آلیاژ فنر تولید کنیم و اینگونه جلوی ورود محصولات چینی و کرهای را بگیریم.
امیدواریم که صنعتگران این دیدگاه را قویتر کنند تا ما بتوانیم موفقتر باشیم. همانطور که برخی نیروهای ما در جبهههای بیرون جان خود را میدهند، ما نیز در حوزه صنعت خوب فعالیت کنیم و بتوانیم صنعتگری خوب و افتخاری برای کشور باشیم و محصول خوبی را تولید کنیم. باید مبحث کیفیت را جدی گرفت. این موضع یک عزم جدی در میان صنعتگران و متخصصان میخواهد.
باید منافع ملی را قبل از منافع شخصی قرار داد
این تفکر و اعتقادات در توسعه صنعت ملی در تمام برنامههای گروه صنعتی امیدفنر مشاهده میشود. از آن جمله میتوان راهاندازی شرکت آلیاژفنر و تولید مفتول در داخل کشور را نام برد.
مهندس عبدالله محمدیپور مدیر عامل کارخانه آلیاژفنر امید و عضو هیات مدیره گروه صنعتی امید در مورد راهاندازی این کارخانه در گروه صنعتی امیدفنر میگوید:
ایمان و اعتقاد به کار ملی همواره از کلیدیترین ویژگیهای جناب آقای محمدیپور مدیر مجموعه و بزرگ ما، بوده و هست. به مرور زمان، این ویژگی در میان تمام افراد مجموعه رسوخ کرده است. به گونهای که بخش بزرگی از برنامهها و تلاشهای ما را در برمیگیرد. از سال 1388 بازار را با دقت بررسی کردیم. اولین موضوع، خطر وابستگی به خارج از کشور بود. ما سال 88 و 89 پیشبینی کردیم که تأمین کالا از منابع اروپایی و آمریکایی با مشکل روبهرو خواهد شد. بعد از آن افزایش قیمت دلار در سال 91 نیز مزید بر علت شد. موضوع دوم، ایجاد تنوع محصول در گروههای خودروسازی بود. پیشبینی میکردیم این موضوع امکانپذیر نخواهد بود که با این حجم بالای تولید، تنوع محصولات گروههای خودروسازی بدون تغییر بماند. حس کردیم که تنوع محصولات بیشتر میشود. با در نظر گرفتن این تغییرات ناگهانی باید 10 مدل مفتول را از خارج از کشور تأمین میکردیم و برای هر کدام نقدینگی ایجاد میکردیم. این اقدامات به حجم سرمایهگذاری بالایی نیاز داشت و انعطافپذیری را در مجموعه پایین میآورد. وقتی حضور شرکتهای چینی و کرهای در بازار مفتول ایران را دیدیم، تصمیم به راهاندازی شرکت آلیاژفنر امید گرفتیم. شرکتی که بتواند ما را در این زمینه خودکفا کند. ابتدای امر، چالشهای بزرگی داشتیم. اینکه بیشترین مشتری این محصول خودروسازان و دیگر شرکتهای فنرسازی بودند؛ کمی ریسک کار را بالا میبرد. اما به هر حال باید خطر را پذیرفت تا بتوان تلاش کرد و نتیجه دید. مجموعه ما نیز اینگونه اقدام کرد. باید منافع ملی را قبل از منافع شخصی قرار داد. بدینصورت مطمئنا نتیجه لذتبخشتر خواهد بود. وقتی آلیاژفنر ایجاد شد؛ به جای 10 سایز، 2 سایز مواد اولیه وارد کردیم و با تغییرات برنامۀ خودروساز توانستیم تغییراتی ایجاد کنیم. این شرکت به میزان قابل توجهی از خروج ارز از کشور جلوگیری کرد. به عنوان یک نمونه سهم یک شرکت کرهای که سالیانه 4 تا 5 هزار تن آلیاژ به ایران میفروخت، الان در اختیار آلیاژ فنر است. در حال حاضر شرکتهای کرهای و چینی به قدری از شرکت آلیاژفنر ناراحت هستند که قیمتهای خود را کاهش دادند تا شاید دوباره بتوانند به بازار ایران برگردند.
هم اکنون میتوانیم 100درصد نیاز فنرسازان داخلی به مواد اولیه و مفتول را تأمین کنیم. در این حوزه به جایگاه تثبیت شدهای رسیدهایم و بازار را از چینیها و کرهایها گرفتهایم. بازار ایرانی باید یک بازار باکیفیت از تولیدات ایرانی باشد. در سالهای تحریم اگر آلیاژفنر امید نبود، به مشکلات بسیار جدی در تأمین مواد اولیه بر میخوردیم که پیامدهای خوبی نداشت. در زمان تحریمها و در مقطعی به صورت ناگهانی برنامه تولید پژو 405 و سمند تغییر کرد و آلیاژفنر در آن زمان ارزش خود را به نمایش گذاشت. ضمن اینکه تولیدات این شرکت، صرفهجویی ارزی برای ایران داشت و بر روی قیمت تمامشده، اثر کاهشی داشتیم. یعنی تولیدات شرکت حدود 35 تا 40 درصد برای کشور صرفهجویی ارزی داشته است. در شرایط فعلی محصول داخلی ایران با محصولات کشورهایی مانند هند و چین 40 درصد اختلاف قیمت دارد.
در حال حاضر شرکتهای کرهای و چینی به قدری از شرکت آلیاژفنر ناراحت هستند که قیمتهای خود را کاهش دادند تا شاید دوباره بتوانند به بازار ایران برگردند.
بحث توسعه و تحقیق برای مدیریت مجموعه صنعتی امیدفنر آن چنان حائز اهمیت است که یک تیم تخصصی و حرفهای در واحد تحقیق و توسعه فراهم آورده است. تیمی که مسئولیت طراحی، شبیهسازی، اجرا و آزمودن تمام محصولات جدید و سفارشی مشتریان را بر عهده دارد.
مهندس امیرحسین محور متولد 1354 فارغالتحصیل کارشناسی ارشد مهندسی مکانیک از دانشگاه صنعتی شریف از همان ابتدا در صنعت خودروسازی حضور داشتند. پس از کسب سوابق کاری ارزشمندی از جمله بازرس کیفی قطعات و مدیر مهندسی در شرکتهای مطرح خودروسازی، هماکنون به عنوان قائم مقام گروه صنعتی امید، در این مجموعه فعالیت دارند. در مورد روند رشد و توسعه واحد کنترل کیفیت و برنامههای آتی گروه صنعتی امید با ایشان به گفتگو نشستیم:
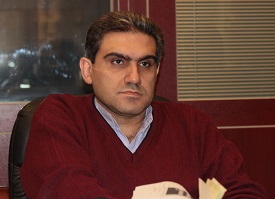
برنامههای آینده گروه صنعتی امیدفنر جهت عملیاتی شدن با چه چالشها و مشکلاتی جدی روبروست؟
صنعت فنر یک صنعت سفارشی است. ما در موارد بسیاری با توجه به نیاز و سفارش مشتری اقدام به طراحی و ساخت فنر میکنیم. اینکه بخواهید برای هر تولید جدید، آزمون و تجهیز مناسب آن را تهیه کنید واقعاً امری نشدنی است. این مشکل نه فقط در صنعت ما بلکه در تمام صنایع قابل تشخیص است. ما هنوز هم بسیاری از تجهیزات مرتبط با آزمون خودرو را نداریم. اگر بخواهیم به کیفیت کار آنگونه که باید، اهمیت دهیم باید تجهیزات با تکنولوژی روز دنیا را فراهم کنیم. اگر بخواهیم با توجه به بودجه و سرمایه سازمان اقدام کنیم، هزینه کلانی بر مجموعه وارد میشود که بدون شک بر قیمت نهایی محصولات تاثیرگذار است. . این در صورتی است که در روند ارزیابی از نظر کیفی ما باید با شرکتهای اروپایی و از نظر قیمتگذاری با شرکتهای چینی رقابت کنیم . این موارد دامنه تولیدات ما را محدود میکند. توانمندی کارشناسان و متخصصان ما امکان طراحی و تولید محصولات بسیاری را میسر میکند اما شرایط مالی و هزینههای بالا در کنترل کیفیت و فراهم کردن تجهیزات، کار ما را در مرحله صحه گذاری طرحها (Validation) محدود میکند. این موضوع اجتنابناپذیر است. آزمون یک ضرورت و الزام است اما مراکز خصوصی به تنهایی قادر نخواهند بود. باید حمایتی از جانب مراکز بالادست صورت بگیرد. بسیاری از آزمونهای ارزشمند و مهم به دلیل همین مشکلات در حال حاضر در داخل کشور انجام نمیشوند. در حال حاضر در کل ایران دستگاه اندازهگیری تنش پسماند فنر وجود ندارد. در کشورهای توسعهیافته و کشورهای اروپایی، دولت و مسئولین بالادست از آزمونها حمایت میکنند. به یاد دارم در پروژهای در مراکش کار میکردم. با تجربهای که داشتم؛ گفتم برای آزمون لنت باید دینامومتر تهیه کنید. این دستگاه بسیار سریع فراهم شد. نکته جالب این بود که کارخانه دستگاه را نخرید. بلکه یک دانشگاه با کمک دولت دستگاه را خریداری کرد و در اختیار صنعت گذاشت. در چنین شرایطی تمام صنعتگران میتوانند از آن آزمون استفاده کنند. فراهم کردن تجهیزات بسیاری از آزمونها توسط بخش خصوصی امکانپذیر نیست. هیچ حمایت و کمکی هم برای ما در این حوزه وجود ندارد. مجبوریم برای بعضی آزمونها هزینههای بسیار بالایی بپردازیم.
در روند ارزیابی کیفی، باید با شرکتهای اروپایی و از نظر قیمتگذاری با شرکتهای چینی رقابت کنیم.
فراهم کردن تجهیزات بسیاری از آزمونها توسط بخش خصوصی امکانپذیر نیست. هیچ حمایت و کمکی هم برای ما در این حوزه وجود ندارد. مجبوریم برای بعضی آزمونها هزینههای بسیار بالایی بپردازیم.
البته با نظر به تمامی مشکلات، در گروه صنعتی امید فنرتا حد امکان اجازه ندادهایم که فرآیند توسعه و بهروزآوری تکنولوژی و تجهیزات متوقف شود. به عنوان مثال در حال حاضر خریداری دو دستگاه تولیدی جدید از کشور آلمان محقق شده است و مطالعات و مذاکرات لازم در خصوص خرید رنج وسیعی از تجهیزات تولیدی و کنترلی از کشورهای آلمان و ایتالیا در مراحل پایانی است. جدیدترین دستگاهی هم که برای آزمون به مجموعه اضافه کردیم، دستگاه ترموگراف است که برای اندازهگیری پروفایل دمایی داخل کورهها مورد استفاده قرار میگیرد. از یک برند معروف هلندی است که از نظر محدوده دمایی و حساسیت دمایی مطابق با آخرین تکنولوژی روز است. البته ما در مورد تمامی دستگاههای ذکر شده ابتدا نیازسنجی کردیم و با برنامهریزی چندینساله برای آینده نسبت به تهیه آنها اقدام کردیم. سعی ما در ابتدای امر، فراهم کردن این دستگاهها از منابع داخلی و حمایت از سازندگان داخلی بود. اما چون میسر نشد، به دنبال برندهای باکیفیت و موفق اروپایی از کشورهای آلمان و ایتالیا رفتیم.
آزمون یک ضرورت و الزام است اما مراکز خصوصی به تنهایی قادر نخواهند بود. باید حمایتی از جانب مراکز بالادست صورت بگیرد. بسیاری از آزمونهای ارزشمند و مهم به دلیل همین مشکلات در حال حاضر در داخل کشور انجام نمیشوند. در حال حاضر در کل ایران دستگاه اندازهگیری تنش پسماند فنر وجود ندارد.
راه حل این مشکل را در چه می بینید؟
علاوه بر حمایت از جانب سازمانها و مراکز مرتبط، خود مجموعهها نیز باید در بخش آزمایشگاه و تجهیزات آزمون با هم متحد شوند. اگر در مورد تجهیزی در شرکت یا کارخانهای سرمایهگذاری شده، این امر مجدداً توسط مجموعه دیگری انجام نگیرد. انرژی و سرمایه خود را برای فراهم کردن تجهیزات جدید متمرکز کنیم. نیاز به یک زنجیره ارتباطی برای کلیه خدمات و فعالیتهای داخلی در حوزه آزمون کاملاً حس میشود. که البته نقش نشریه "فناوری آزمون و اندازه گیری" به عنوان یک رسانه تخصصی بسیار حائز اهمیت است.
بحث کنترل کیفیت را باید جدی بگیریم. آزمون و آزمایشگاه قلب تپنده صنعت است. فرهنگ غلطی که متأسفانه در برخی ابعاد صنعت ما به چشم میخورد، افزایش تولید بدون اطمینان از کیفیت است. باید این نگاه را عوض کنیم. تولید تنها در صورتی ارزشمند و قابل ستایش است که مطابق با استانداردهای روز باشد.
باید در هر شاخه صنعت به دنبال اتحاد و هماهنگی بین مراکز آزمون باشیم. وجود مراکز تخصصی آزمون موجب تسهیل امور در این زمینه است. در صنعت فنرسازی کشور، در حال حاضر مجهزترین و پیشرفتهترین تجهیزات و دستگاههای مورد نیاز در گروه صنعتی امیدفنر یافت میشود. در حقیقت در سال 1389 با نیت تبدیل شدن به یک مرکز تخصصی و مرجع در زمینه آزمونهای مرتبط با صنعت فنر استاندارد 17025 را اخذ کردیم . اما آنقدر درگیر چالشهای بیشمار شدیم که فعلا موضوع را مسکوت گذاشتهایم. البته پتانسیل آن کاملاً وجود دارد، سرمایهگذاریهای بسیاری نیز شده است و این موضوع از جانب ما بسیار مطلوب است. در حال حاضر کلیه امکانات و تجهیزات فقط در داخل گروه صنعتی و محصولات خودمان استفاده میشود. اما اینکه به عنوان مرکز تخصصی آزمون فنر در کشور و یا حتی منطقه باشیم را دنبال میکنیم و جزو اهداف ما است.
نیاز به یک زنجیره ارتباطی برای کلیه خدمات و فعالیتهای داخلی در حوزه آزمون کاملاً حس میشود. که البته نقش نشریه "فناوری آزمون و اندازه گیری" به عنوان یک رسانه تخصصی بسیار حائز اهمیت است.
در مورد تعاملات گروه صنعتی امیدفنر با کشورهای دیگر - چه در حوزه علمی و چه تامین تجهیزات- چه اقداماتی انجام گرفته است؟
همواره سعی کردیم خودمان را با برترینهای جهانی بسنجیم. معیار و میزان برای ما حرکت در مسیر تکنولوژی روز دنیاست. شرکت امیدفنر سالهاست که عضو انجمن تکنولوژی فنر انگلستان است. برای عضویت شرکت آلیاژفنر در یک انجمن مفتولسازی اروپایی نیز اقداماتی صورت گرفته است. در سال گذشته بازدیدها و مذاکرات بسیار سنگینی با بیش از 7 شرکت مطرح فنر ساز و مفتول ساز داشته ایم که انشاله بزودی مذاکرات نهایی و الگوی همکاری بین المللی شرکتهای گروه مشخص خواهد شد و در اختیار هر دو شرکت امید فنر و آلیاز فنر قرار خواهد گرفت .
این همکاریهای جهانی نه تنها راه تبادل دانش و تکنولوژی را هموارتر میسازد، بلکه نام گروه صنعتی امیدفنر نیز در کنار بزرگترین و مطرحترین برندهای صنعت فنر و مفتول در جهان قرار میگیرد. به علاوه قدرت ما را در بازاریابی نیز افزایش خواهد داد.
همواره سعی کردیم خودمان را با برترینهای جهانی بسنجیم. معیار و میزان برای ما حرکت در مسیر تکنولوژی روز دنیاست.
با توجه به سالها حضور موفق در صنعت، از دیدگاه تخصصی و فنی چه عواملی را در توسعه مجموعه در نظر میگیرید؟
برای پرداختن به توسعه، ابتدا باید تعریف جامع و کاملی از این واژه ارائه دهیم. گاهی اوقات توسعه دارای فرآیند پیچیدهای است و گاهی فرآیند سادهای دارد. مزیتی که در سازمان ما وجود دارد این است که دائماً در حال رصد تحولات صنعت فنرسازی هستیم و برهمین اساس میتوانیم جزییات پیش بینی صنعت فنر و مفتول را تا سال 1403 در اختیار شما قرار دهیم.
نقطه شروع برای یک پیشرفت، پیشبینی کردن وضعیت صنعت داخلی و خارجی است. بعد از این پیشبینی میتوان اهداف را به قدمهای کوتاهمدت تقسیمبندی کرده و سپس نیازها را شناسایی کرد. ما به صورت دائم در نمایشگاههای مرتبط از جمله نمایشگاه صنعت وایر آلمان و شانگهای چین شرکت میکنیم. اینگونه میتوان بین صنعت داخلی و خارجی یک تعادل برقرار کرد. به طور مثال ما پیشبینی کردهایم که در 5 سال آینده فنر خاصی جایگزین فنرهای فعلی خواهد شد که با تجهیزات موجود قابل تولید نیست. بنابراین از هماکنون تیم مالی ما با بانک برای خرید تجهیزات وارد مذاکره شده است تا زمینه برای خرید فراهم شود. تیم ما به صورت دائم تمام اطلاعات را رصد کرده و آنالیز میکند و پس از آن اولویتبندی کرده و آن را به برنامههای مقطعی و قابل اجرا تبدیل میکند.
به صورت کلی در شرکت ما قانون نانوشتهای در هیأت مدیره مصوب شده که براساس آن هر سال 2 تا 3 دستگاه را باید جایگزین کنیم. تا چند سال گذشته که کشور تحریم بود، در خصوص جایگزینی دستگاه مشکلاتی وجود داشت و سعی کردیم که با محدودیتها کنار بیاییم ولی در یک سال اخیر که این مشکلات مرتفع شده است. به سرعت نسبت به تأمین تجهیزات مورد نیاز اقدام کردیم.
آینده صنعت فنر را در بازار جهانی و حوزه صادرات چگونه پیش بینی میکنید؟
واقعیت این است که در سالهایی که تحریم برقرار بود، موقعیتهای بسیاری را از دست دادیم. بسیاری از فرصتهای صادراتی که میتوانستیم داشته باشیم از بین رفته است. زمانی که شرکتهای مطرح دنیا در حوزه فنرسازی در کشورهای صنعتی همسایه مثل ترکیه سرمایهگذاری کردهاند، دیگر جایی برای ما باقی نمیماند و پیدا کردن کشوری به عنوان بازار هدف صادراتی بسیار مشکل است. بنابراین ما از چرخه تجارت جهانی عقب افتادهایم. در حال حاضر شاید موضوع صادرات تنها در حالتی محقق میشود که کلان باشد. اگر در حوزه صادرات خودرو اقداماتی صورت بگیرد، به عنوان اولین شرکت تولیدکننده فنر برای خودروسازان کشور محصولات ما نیز وارد چرخه صادرات خواهد شد.