حمید صنعت فرد؛
گامی بلند از مهندسی معکوس
تا مهندسی محصول
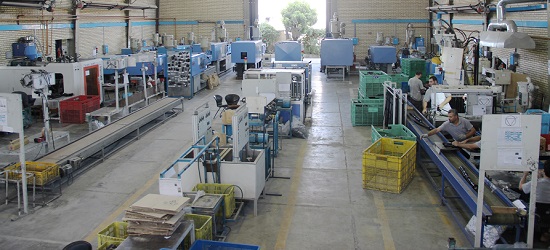
شرکت حمیدصنعت فرد، در زمره آن شرکتهایی است که با اتکا به دانش مهندسی، در زمینه نوآوری و خلق محصولات جدید در صنعت قطعهسازی پیشآهنگ میباشند. یکی از کاستیها در ساخت قطعات خودرو در داخل کشور، بومی نشدن دانش و انتقال ناقص فناوریها میباشد که بنا به تقلید از خودروسازان صاحب تکنولوژی چون پژو و کیا اتفاق افتاده است. به عنوان نمونه، بنا به شرایط خاص محیطی و پاشش نمک در فصول سرد سال در جادههای اروپا، آزمون خوردگی برای خودروهای تولیدی آن سامان بسیار پر اهمیت است؛ این در حالی است که در شرایط آب و هوایی و تنوع جادههای ایران، پاشش گل و لای، افزایش گرد و غبار و تعدد دستاندازها چالش اصلی رانندگی در اینجاست. در عین حال برنامه آزمون بیشتر قطعات، کپی کاملی از مشخصات آزمون قطعات خودروسازان خارجی است و بومی نشده است. شرکت حمیدصنعت فرد، از شرکتهای سرآمد است که با الگوبرداری از شرایط مشابه جهانی و بر اساس تفکر مهندسی، قائل به تغییرات در طراحی و ساخت قطعات است؛ به گونهای که شرایط اقتصادی تولید قطعه، در دسترس بودن فناوریهای مرتبط با تولید و آزمون و توانمندیهای داخلی در نظر گرفته شود. بدیهی است لزوم حمایت و انتشار این فرهنگ در دیگر شرکتهای تولیدی داخلی و در بخشهای طراحی مهندسی خودروسازان، توسط مدیران صنعت کشور بر کسی پوشیده نیست.
در ادامه توجه شما را به گزارشی که توسط نشریه "فناوری آزمون و اندازهگیری" از فعالیتهای شرکت حمیدصنعت فرد و دیدگاه مدیران ارشد آن تهیه شده جلب میکنیم. بدیهی است، آنچه در این گزارش آمده، برآمده از نظرات مدیران ارشد این شرکت و حاصل گفتگوی ما با مدیر عامل و قائم مقام ایشان است و از همه رقبا و کسانی که به گفتههای این عزیزان انتقاد دارند، دعوت میشود در همین رسانه، نظر خود را اعلام کنند. امیدواریم چالشهای مطرح شده در این گزارش همچون مقایسه باکهای پلیمری و فلزی، در فضایی سالم و با هدف بهبود کیفی صنایع داخلی در نگریسته شود.
تاریخچه شرکت حمیدصنعت
شرکت حمیدصنعت فرد در سال 1374 تأسیس شد و در سال 1375 اولین قرارداد خود را با خودروسازان منعقد کرد و اکنون با اکثر سازندگان خودرو طرف قرارداد است. در ابتدا این شرکت قطعات پلیمری و فیلترهای سوخت را تولید مینمود، ولی در حال حاضر مجموعههای قطعات خودرو، به ویژه مجموعههای سوخترسانی را نیز تولید میکند.
--------------
شرکت برتر طراحی در گروه خودروسازی سایپا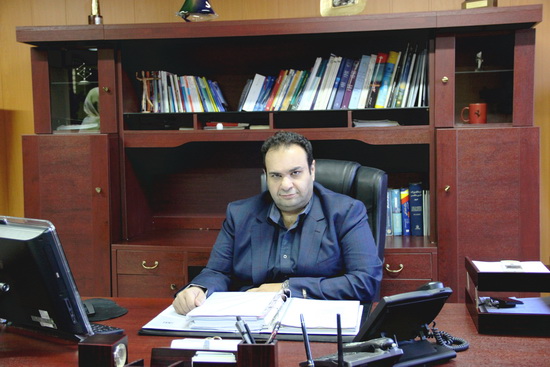
مهندس فرید منتظر؛ مدیر عامل شرکت حمیدصنعت فرد در رابطه با چگونگی شکلگیری این شرکت و پروژههای انجام شده گفت: از آنجا که در صنایع خودروسازی به نظر میرسد آینده از آنِ شرکتهایی با قابلیت طراحی بالا خواهد بود، شرکت حمیدصنعت از سال 1382 با این رویکرد فعالیت خود را در حوزه طراحی و مهندسی تحقیق و توسعه (R&D) گسترش داد؛ به نحوی که شرکت حمیدصنعت فرد در حال حاضر شرکتی دانشمحور و متکی به توانمندی طراحی و مهندسی خود است.
این شرکت در سال 1382 به منظور ارائه خدمات شایسته به مشتریان عمده خود یعنی خودروسازان اقدام به ایجاد واحد طراحی مهندسی نمود. این در حالی است که تا پیش از آن بیشتر شرکتهای طرف قرارداد با خودروسازان، با دریافت نقشه قطعات از مشتری و با کمک تکنیکهای مهندسی معکوس، قطعات مورد نیاز را تولید مینمودند. مدیران ارشد شرکت حمیدصنعت، با تمرکز بر این نقطه ضعف، استراتژی جدیدی در شرکت ایجاد کردند و با تکیه بر ظرفیت و قابلیت طراحی خود توانستند برای اولین بار در کشور محصولات جدیدی به خودروسازان ارائه دهند. این محصولات و پیشنهادهای جدید قابلیت رقابت جدیدی برای خودروسازان فراهم آورد. معنی این گفته آن است که با استفاده از دانش و شناخت بالای پلیمرهای جدید، محصولاتی تولید شدند که ارزانتر، مرغوبتر، سبکتر و با دوامتر طراحی و ساخته شد و در نهایت برای مشتری و مصرفکننده نهایی رضایت خاطر بیشتری فراهم نمود. تلاش و درایت کارکنان شایسته شرکت حمیدصنعت فرد باعث شد این شرکت به عنوان یکی از شرکتهای برتر گروه خودروسازی سایپا، در حوزه طراحی و مهندسی طی دو دوره متفاوت به عنوان شرکت برتر انتخاب شود. این در حالی بود که شرکتهای بزرگ دیگری به عنوان شرکت برتر از نظر تأمین و یا از دیدگاه کیفیت شناخته شدند. شاید توانایی طراحی در این شرکت، یاداور افسانه مایداس باشد. مایداس، هر فلزی را که لمس مینمود، به طلا تبدیل میشد و شرکت حمیدصنعت به هر فلزی که دست میزند به پلیمر تبدیل میشود!
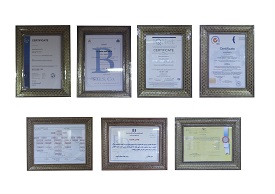
ایشان ضمن اشاره به افزایش ظرفیت و قابلیتهای طراحی و مهندسی طی سالیان اخیر در شرکت حمیدصنعت گفت: در دنیای کنونی همه چیز به سمت سبکتر شدن پیش میرود و رویکرد توسعه دانش و فناوری در همه عرصهها مشهود است. شاید مهمترین و مشهودترین نمود آن را بتوان در صنایع خودروسازی مشاهده کرد. خودروهای اولیه، بدنه فلزی از جنس استیل داشتند و سپس در نسلهای بعد استفاده از آلومینیوم باعث سبکتر شدن خودرو و در نتیجه کاهش مصرف انرژی گردید و در حال حاضر مواد پلیمری میتواند رقیب بهتری برای آلومینیوم باشد. با پیشرفت تکنولوژی، خواص مکانیکی پلیمرها بهبود یافته و همین نکته باعث استفاده گستردهتر پلیمرها در صنایع مختلف و به ویژه صنعت خودروسازی شده است.
یکی از شاخصهای مهم توانمندی طراحی و مهندسی شرکت حمیدصنعت، نسبت بالای پرسنل تحصیل کرده به کل افراد شاغل در این شرکت است. قابلیت بالای طراحی، نقطه قوت این شرکت در رقابت با سایر رقبا بوده است. تاکنون بیش از چهل قطعه و مجموعه برای اولین بار باز طراحی شده است و در لیست قطعات تولیدی شرکت حمید صنعت قرار گرفته است.
مهندس منتظر طراحی و ساخت محصولات این شرکت را از گذشته با کیفیت قابل قبول توصیف کرده و بیان داشت: در شرکت حمیدصنعت، در همه پروژهها، فرایند امکانسنجی اولیه با طمانینه و صرف وقت کافی گاه تا یک سال طول میکشد تا اینکه تشخیص داده شود پروژه منطقی است. به عبارت دیگر به تمام سوالاتی که ممکن است در آینده مشتری با آن مواجه شود، اندیشیده میشود و پاسخ درست، منطقی، علمی و قابل دفاع برای آنها یافت میشود. حصول موفقیت در این راه، چراغ سبزی برای طرح موضوع نزد مشتری است. در صورتی که پروژه قابل دفاع نباشد، حتی با وجود درخواست مشتری، هیچگاه محصولی تولید نخواهد شد.
مورد دیگر لزوم همگرایی شرکتهای همسو با یکدیگر و ایجاد شرکتهای بزرگ برای کاهش هزینههای سربار و طراحی و همافزایی تکنولوژیک در صنعت خودرو است. این امر توسط معاون محترم ریاست جمهور و وزیر محترم صنایع نیز تاکید شده است.
واقعیت این است که از حدود پانصد قطعهساز فعال در زنجیره تامین ایرانخودرو و سایپا، شرکت حمیدصنعت از معدود شرکتهایی است که قابلیت طراحی بالایی دارند. بارها این شرکت از سوی خودروسازان مورد ارزیابی طراحی قرار گرفته و در حقیقت اولین شرکتی است که از سوی شرکت سازهگستر سایپا از نظر طراحی و فناوری ارزیابی شده است. گفته مدیران شرکت این است که ما فنّاوری را ایجاد میکنیم.
مهندس منتظر در بیان توانمندی شرکت در مقایسه با سایر رقبا بیان داشت: مزیت رقابتی شرکت حمیدصنعت، نسبت به سایر رقبا، قابلیت بالای طراحی و سیستم چابک آن است. طراحی خوب؛ اقتصادی، منطبق بر استاندارد و الزامات مشتری، قابلیت برآوردهسازی آزمونهای عملکردی و دوام را داراست و نهایتاً سبب رضایت مشتری نهایی میشود. یک طرح خوب، الزاماً به معنای تبدیل قطعهای فلزی به پلیمری نیست. بلکه در طراحی باید همه جوانب آن اندیشیده شود. مانند ویژگیهای عملکردی، استحکام، انطباقات، ابعاد و حتی ویژگیهای بصری و ظاهری. مثلاً در طراحی اولیه لوله پرکن باک بنزین، به دلیل صاف بودن درب آن، نازل پمپ بنزین در هنگام بنزین زدن رها شده و ثابت نمیماند و همواره نارضایتی مشتری را به همراه داشت. با تلاش مهندسین شرکت حمیدصنعت، طرح لوله پرکن به گونهای تغییر کرد که با ایجاد زوایای خاص در قطعه، قرارگیری نازل بر دهانه لوله پرکن ثابت مانده و نیازی به نگهداری دائم نازل پمپ بنزین توسط اپراتور ندارد. همین تغییر به ظاهر ساده، کل فناوری و طراحی قطعه را تغییر داد.
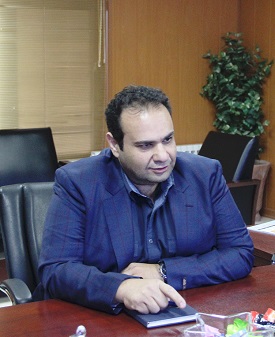
در حقیقت وظیفه شرکتهای قطعهساز این است که قطعات آینده را طراحی کنند. امروزه با فناوری سال 2016، وظیفه خودروسازان طراحی همه قطعات و مراحل ساخت آنها نیست یا نقشه قطعات را تهیه نمایند و نمونه بدهند و به قطعهسازان الزامات ساخت قطعه را ارائه نمایند. بلکه با فراهمآوری بسترهای مناسب، زمینه ارتقای دانش و توانمندی مهندسی را در بدنه کارشناسی قطعهسازان فراهم نموده و بدین طریق کلیه مراحل طراحی و ساخت قطعات و فرآیندهای مربوطه را به آنان واگذار میکنند. با این نگرش شرکت حمیدصنعت فرد توانسته است میزان فروش قطعات و محصولات خود را از سال 1386 تاکنون ده برابر نماید. این شرکت نگاه به آینده دارد و از تمام پتانسیلهای موجود بهره میگیرد. شرکتی که به طراحی و به دانشبنیان بودن توجه کند نهایت سود را هم میبرد.
مهندس منتظر در نحوه پذیرش الگوی طراحی قطعات در شرکتهای خودروساز بیان داشت نکته اساسی دیگر بحث مالکیت معنوی در خودروسازهاست. خودروسازها نمیتوانند بپذیرند، شرکتهای طراح، دارای دانش بالاتر از خودروسازها هستند. این امر منجر به لحاظ نشدن مالکیت معنوی برای این شرکتهای دانشبنیان در قراردادها شده که بزرگترین خطر برای ادامه حیات شرکتهایی همچون حمیدصنعت فرد است و آینده آنها را به مخاطره میاندازد. اگر بحث مالکیت معنوی برای قطعهساز مدیریت نشود، آینده قطعهسازی در ایران از بین خواهد رفت. این منطقی، شرعی، اخلاقی و حتی قانونی نیست که شرکتی طراحی کند، طرح قطعه را توسعه دهد، یک نقشه کامل تهیه نماید و برخی کارشناسان مشتری، این نقشه آماده را دو دستی به رقیب تقدیم نمایند. متاسفانه در قراردادهای شرکت سازهگستر اجازه ارائه طرح به هر شرکت و فرد دیگری از سوی کارفرما مجاز شده که این امر نمیتواند عادلانه باشد.
مجموعه شرکتهای حمیدصنعت، تولیدکننده فیلتر سوخت، لولههای سیستم انتقال سوخت و شیرهای کنترل بخارات؛ شرکت راویان نور، تولید کننده پمپ و گیج و ملحقات آن و شرکت تکلان، تولیدکننده باک فلزی، سه شرکتی هستند که به زودی با ایجاد یک کنسرسیوم به صورت واحد عمل نموده و کل مجموعه سوخت از نازل بنزین تا موتور را تولید میکنند.
نمونههایی از پیشنهادهای شرکت حمیدصنعت به خودروسازان و تاثیرات اقتصادی و زیست محیطی آنها
مهندس مسعود ملکی قائم مقام مدیرعامل و مدیر مهندسی شرکت حمیدصنعت فرد در بیان نمونههایی از محصولات این شرکت خاطرنشان کرد: در ابتدا لوله پرکنهای سوخت پراید، از نوع ترکیب فلزی-لاستیکی بود که استاندارد یورو یک را برآورده نمیکرد و وزن آن حدود 3.7 کیلوگرم بود. در واحد طراحی مهندسی شرکت با در نظر گرفتن الزامات خودروسازان و مقایسه با محصولات مشابه در خودروهای روز دنیا، با استفاده از مواد پلیمری، این قطعه بازطراحی شده و به خودروساز پیشنهاد گردید. با توجه به کاهش قیمت بیش از پنجاه درصد، کاهش وزن به پانصد گرم یعنی حدود یک ششم وزن اولیه و قابلیت کیفی در حد استاندارد یورو چهار، بدیهی بود که مشتری با این همه مزایا و پس از انجام آزمونهای راستیآزمایی کیفی، این قطعه پلیمری را جایگزین قطعه لاستیکی- فلزی اولیه نماید.
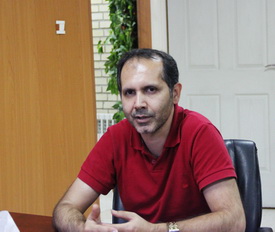
از دیدگاه زیست محیطی، با کاهش وزن قطعه به یک ششم، یعنی کاهش 2.3 کیلوگرمی وزن خودرو مصرف سوخت نیز کاهش مییابد. میدانیم که به ازای هر 100 کیلوگرم تغییر در وزن خودرو در هر 100 کیلومتر پیمایش یک لیتر مصرف سوخت تغییر خواهد کرد. پس در مقیاس کلان برای میلیونها خودرو در پیمایش سالیانه، میلیونها لیتر مصرف سوخت کاهش مییابد و این یک اقدام بسیار مفید زیست محیطی است.
نکته قابل تامل آن است که همیشه رویکرد جایگزینی فلز با مواد پلیمری صحیح نیست. گاه این جایگزینی باعث میشود مزیتهای مورد نیاز برآورده نشود. به عنوان نمونه، در مورد باکهای سوخت، در برخی نقاط دنیا همچون اروپا باکها پلیمری و در برخی جاهای دیگر همچون آمریکا و ژاپن باکها فلزی مورد استفاده قرار میگیرند. دلیل این امر گستره دمایی محیطهایی است که این خودروها قرار است در آن مناطق استفاده شوند. به عنوان مثال مواد پلیمری به کار رفته در ساخت باکهای پلیمری، از مقصد کوههای سبلان تا بندرعباس، تحمل این اختلاف دمای حدود 50 درجه را در مدت کم ندارند. در ژاپن و آمریکا با توجه به گستردگی آب و هوایی، چنین اختلاف دمایی کاملاً ممکن و قابل حصول است و در این کشورها عمدتاً از باک فلزی استفاده میشود تا از خزش پلیمر ناشی از اختلاف دما در باک در مدت کم و در نتیجه خطرات احتمالی پیشگیری شود. بدیهی است که استفاده از مواد پلمیر پلیآمیدی بدلیل قیمت بالا مقرون به صرفه نیست. پس این اندیشه که مواد فلزی را تا جای ممکن به مواد پلیمری سبکتر تغییر داد، همیشه صحیح نیست و باید جمیع شرایط اقتصادی، عملکردی، زیست محیطی، ارزی، ماشینآلات و فناوری تولید، دانش فنی و نظایر آنها را در نظر گرفت.
نمونه دیگری که مهندس ملکی در ادامه به توضیح آن پرداختند فیلتر بنزین در خودروهایی با پمپهای داخل باک (In-Tank) و بیرون از باک بود. طراحی این محصول در عین حال، نیاز به دو یا سه عدد لوله اضافه و چند بست وکانکتور دارد تا این فیلتر را از پمپ بنزین مجزا نماید. همین نکته باعث افزودن قیمت حدود چهل یا پنجاه هزار تومان به هزینه تمام شده خودرو میشود. در طراحی پیشنهادی شرکتهای حمیدصنعت و راویان نور با داخل باک قرار دادن فیلتر بنزین، چهار نقطه اتصال سوخت که همیشه نقاط خطرناکی هستند از بین میرود؛ زمان تعویض فیلتر به خاطر استفاده از کاغذ لانگ لایف، به جای 20 هزار کیلومتر، چهار برابر یعنی 80 هزار کیلومتر افزایش یافته و از نظر اقتصادی نیز باعث کاهش حدود چهل هزار تومان از قیمت تمام شده سیستم سوخترسانی میشود.
در حال حاضر با در نظر گرفتن استانداردهای یورو یک تا یورو چهار، همگام با سایر کشورهای پیشرفته دنیا، که دیدگاه غالب، طراحی خودروهای سبکتر با مصرف سوخت کمتر و الزامات زیستمحیطی سختگیرانهتر است شرکت حمیدصنعت فرد نیز توانسته است با توسعه زیرساخت های مهندسی و کسب دانش روز دنیا گام های مهمی در این مسیر بردارد.
بخش تحقیق و توسعه
مهندس مسعود ملکی در تشریح ساختار مهندسی در شرکت حمید صنعت بیان داشت: بخش تحقیق و توسعه به صورت مجزا از سایر بخشها و به ویژه مستقل از ذائقه و خواست مشتری نیست. اینگونه نیست که نفرات فعال در بخش R&D مستقل از واحدهای تضمین-کیفیت و کنترل کیفیت باشند؛ بلکه کارها به صورت تیمی انجام میشود و همه پرسنل شرکت در فرآیند طراحی و تحقیق نقشی دارند. این که اولویتها چگونه بررسی شود، به نیاز مشتری، کاهش قیمت مورد انتظار در پایان پروژه، امکانات قابل دسترس در کشور و نظایر آن بستگی دارد. شرکت حمیدصنعت، رسالت خود را تولید قطعه خودرو قرار داده است، در قطعات خودرو به قطعات پلیمری گرایش دارد و در قطعات پلیمری هم بیشتر تمرکز آن بر تولید قطعات سیستم سوخترسانی است.
مدیر مهندسی شرکت تاکید کردند؛ همه پرسنل از مدیر عامل تا پایینترین رده سازمانی، هر ایده و یا طرحی داشته باشند، حتی در حد یک حرف، یک ایده و یا یک شنیده، آن را در سازمان مطرح مینمایند. استقرار یک سیستم جامع نرمافزاری برای جمعآوری تمام پیشنهادات از تمام بخشها و واحدهای شرکت به بروز اینگونه ایدهها کمک شایانی نموده است. شرکت حمیدصنعت، شرکتی دانش محور است و در آن کلیه مبادلات نوشتاری سازمان شامل انبار و مالی و مدیریت و حسابداری و تضمین کیفیت و کنترل کیفیت، بصورت الکترونیکی و بدون کاربرد کاغذ (paperless) انجام میشود. هر ایدهای که مطرح شود، ابتدا از نظر هم سویی با فعالیتها و رسالت شرکت در تیم مدیریتی بررسی شده و در مرحله بعد با استفاده از اصول الگوبرداری (Benchmark) مطالعه میشود که با این ایده در بقیه شرکتها و حتی کشورها چه برخوردی انجام شده است. به عنوان نمونه در طراحیهای مربوط به شرکت کیا موتورز، مرسدس بنز و ... چگونه است. به همین منظور استفاده از نمایشگاههای تخصصی خارج از کشور نظیر نمایشگاه اتومکانیکا، تست و هر نمایشگاهی به ویژه در کشورهای صاحب فناوری در دستور کار قرار دارد. در گام بعدی شرایط بومی داخل کشور نظیر قابلیت تولید، ماشینآلات مربوطه، حساسیت مشتری به نتایج ایده و تغییر طرح، بررسی میشود. گاه پیشنهاد به مشتری، در سطح پردازش ذهنی او قرار نمیگیرد. به عنوان نمونه استفاده از موتور هیبرید در سایپا نمیتواند در شرایط کنونی مطرح شود. در حال حاضر شرکت سایپا از ایدههایی که منجر به کاهش قیمت محصول نهایی شود و الزامات زیستمحیطی و همچنین قوانین مربوطه را رعایت نماید استقبال میکند. کل مراحل بالا "امکان سنجی اولیه" نامیده میشود. سپس در مرحله بعد با لحاظ کردن ابعاد مالی و فنی، نظیر قابلیت تولید در داخل شرکت و وجود یا در دسترس بودن فناوریهای مربوطه و ماشینآلات، زمان تصمیمگیری فرا میرسد. در صورت تایید، طرح مربوطه به مشتری پیشنهاد شده و پس از اخذ تاییدیه وی در مراحل بعدی نهایتاً کار تا تولید انبوه پیش میرود. به عنوان مثال بذر ایده پروژه استفاده از فیلترهای (In tank) حدود دو سال پیش در نمایشگاه اتومکانیکا در ذهن یکی از مدیران شرکت شکل گرفت، یک و نیم سال پیش در شرکت حمیدصنعت مطرح شد، ده ماه پیش نیز در سازهگستر عنوان گردید و الان در فاز تولید آزمایشی قرار دارد.
پس از تغییر طرح یک قطعه، به عنوان مثال هنگامی که قسمتهای فلزی با مواد پلیمری جایگزین میشوند، با توجه به وجود استانداردهای بسیار سختگیرانه صنایع خودرو و با اتکا به دانش و تجربهای که در شرکت حمیدصنعت، طی سالیان دراز انباشته شده، آزمونهای مربوطه نیز طراحی شده و با هماهنگی مشتری صحهگذاری میشود.
در هنگام نیاز با استفاده از تجهیزات آزمون موجود در آزمایشگاهِ شرکت حمیدصنعت مطابق با الزامات و استانداردهای موجود، آزمونهای مورد نظر به انجام رسیده و گزارشات آن جهت بهرهبرداری در اختیار واحدهای مهندسی و کنترل کیفیت قرار میگیرد. بدیهی است تجهیزات آزمون مربوطه توسط امور متدِ مشتری بررسی و صحهگذاری شدهاند. برای انجام سایر آزمونها، از آزمایشگاههای بیرون از شرکت و حتی خارج از کشور خدمات گرفته میشود. به عنوان نمونه آزمونهای مربوط به باک فلزی در کشور چک انجام شده است. ضمن این آزمونها، از امکانات و دانش و تجربه شرکتهای خارجی هم استفاده میشود.
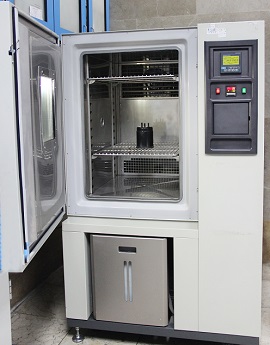 |
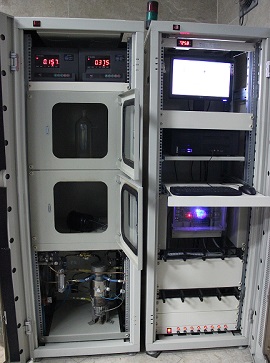 |
چمبر شرایط محیطی |
موقعیت جغرافیایی تپه سنگ بزرگ میرجاوه |
پروژه فلزی کردن باکهای پلیمری
مهندس مسعود ملکی در خصوص پروژه فلزی کردن باکهای پلیمری خوردو ضمن خاطرنشان کردن رسالت شرکت حمیدصنعت در بهینهسازی فناوری قطعات خوردو بیان داشت: در این راستا، گاهی لازم میشود به منظور بهینهسازی قطعات، بخش یا قطعه فلزی به پلیمری تبدیل شود یا بالعکس. گاهی نیاز است که بسته به شرایط موجود، قطعات پلیمری به فلزی تغییر یابند. در واقع این مسیر، یک راه دو طرفه است. از آنجا که شرکت حمیدصنعت، شرکتی طراح محور است رویکرد کنونی شرکت، تغییر طرح باکهای پلیمری به باک فلزی است و به همین منظور با کمک و هماهنگی شرکت توف در کشور چک، آزمونهای مربوطه که در ایران قابل انجام نیست پیگیری شده و نمونههای باک فلزی که در شرکتهای حمیدصنعت و تکلان طراحی و ساخته شده است برای آزمون و صحهگذاری به شرکت توف فرستاده شده است. از مزایای باک فلزی علاوه بر تحمل بهتر در برابر آتش، جلوگیری از تغییر شکل و خزش بدلیل اختلاف دمای زیاد در زمان کم است. طرح باک پلیمری برای اروپا که چنین تغییرات دمایی ندارد البته مناسب است ولی شرایط بومی کشور ما با اروپا یکسان نیست. در برخی از مناطق ایران، میزان رطوبت هوا صفر و در برخی نقاط دیگر مانند نواحی ساحلی میزان رطوبت نود در صد است و در برخی از مکان ها شرایط مه نمکی یا اسیدی وجود دارد. واقعیت این است که در صورت بومیسازی، همیشه تکنولوژی اروپایی برای کشور ما مناسب نیست و اگر طرح یک قطعه برای اروپا بهترین باشد، لزوماً برای سایر کشورها طراحی مناسبی نیست. از سوی دیگر باکهای فلزی در مقایسه با باکهای پلیمری کاهش وزن محسوسی هم ندارند. علت این است که در باکهای پلیمری برای جلوگیری از نفوذ و نشتی سوخت به بیرون باید از باکهای چندلایه استفاده شود. به عنوان مثال باک خودروی پژو 405 پلیمری 5 کیلوگرم وزن دارد، این در حالی است که نوع فلزی آن هم حدود 5.5 کیلوگرم است. در مقام مقایسه لوله پرکن پلیمری یک ششم لوله پرکن فلزی وزن دارد و تغییر طرح فلزی به پلیمری کاملاً موجه است. از نظر اقتصادی هم باک فلزی حدود هشتاد هزار تومان ارزانتر است. از طرفی، مواد اولیه باک پلیمری را تنها باید از برندی خاص مانند توتال (total) تهیه نمود. زیرا شرکتهای پتروشیمی داخل کشور امکان تولید این ماده را ندارند. این همان حلقه مفقودهایست که در فرآیند ایدهپردازی و امکانسنجی شرکت حمیدصنعت از ابتدا دیده میشود. حال با تغییر باک به نوع فلزی امکان استفاده از صنایع فولاد داخلی هم فراهم است و به عبارتی اینجا بومیسازی اتفاق میافتد و ارزبری هم از بین میرود. از همه موارد یاد شده که صرف نظر شود از دیدگاه زیست محیطی، در باکهای پلیمری برای گذراندن معیارهای یورو پنج باید از باک شش لایه استفاده شود تا بتوان پارامترهای نفوذ، خزش و ... را کنترل نمود. ولی در صورت استفاده از باک فلزی به راحتی میتوان الزامات استانداردهای مربوطه را برآورده ساخت.
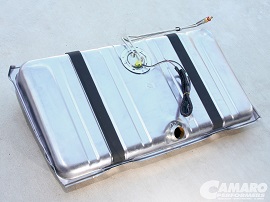 |
حتی در خودروهای اروپایی؛ اگرچه برای کلاس خودروهای متوسط به پایین از باک پلیمری استفاده میشود، ولی در خودروهای لوکس باک پلیمری به کار برده نمیشود. در واقع خودروساز ریسک کاهش ایمنی خودرو را با استفاده از باک پلیمری نمیپذیرد. پس خودروسازهای لوکس اروپایی هم از باک فلزی استفاده میکنند.
ایشان در ادامه خاطر نشان نمود: در کشورهای آسیای شرقی و جنوب شرقی مانند چین، ژاپن و کره، به ندرت از باک پلیمری استفاده میشود. مهمترین دلیل، آن است که مواد اولیه، باید از اروپا وارد شود، حال آنکه ورق به صورت محلی در آن کشورها تولید میشود. بزرگترین تولیدکنندگان ورق خودرو در آسیا مستقر هستند. شرکت کرهای پوسکو، بزرگترین تولیدکننده ورق خودرو در دنیاست. بنابراین شرکتهای خودروساز در آن کشورها، قطعات را به گونهای طراحی میکنند که صنعت پیشرفته فولادسازی داخلی حمایت شود. متاسفانه در کشور ما دقیقاً برعکس عمل شده است و مثلاً با وجودِ داشتن صنعت فولاد، باک پلیمری و نه باک فلزی تولید میشود. البته در گروه سایپا خوشبختانه دیدگاه بسیار مثبتی وجود دارد و نسبت به ارائه پیشنهادات مناسب استقبال میشود.
مهندس ملکی یکی دیگر از مشکلات عمده در صنعت خودروی کشور را عدم وجود یک دیدگاه و برنامه کلان استراتژیک دانسته و بیان داشت: انتقادی که در حال حاضر میتوان به صنایع خودروسازی وارد نمود عدم وجود دیدگاه استراتژیک کلان است. سوالات اساسی که در این زمینه وجود دارد آن است که اهداف و برنامههای کلان صنایع خودروسازی در کشور چیست؟ کدام صنایع و مشاغل را مورد حمایت قرار میدهد؟ برنامهها و اهداف کلان اقتصادی آن در آینده چگونه ترسیم شده است؟ و ارتباط آن با سایر صنایع چگونه شکل گرفته است؟ میتوان گفت پاسخ مشخص و روشنی وجود ندارند. گفته میشود صنعت خودرو موتور محرک و لوکوموتیو سایر صنایع است. این گفته در صورتی مصداق دارد که سایر صنایع هم نقش واگنهای پشت سر را به درستی ایفا کنند، در غیر اینصورت حرکت لوکوموتیو به تنهایی ارزشی ندارد. اگر لوکوموتیو صنعت، خودرو باشد، یک واگن آن ورق چهار محال و بختیاری و واگنهای دیگر، شرکت حمیدصنعت و یا تمام شرکتهای قطعهسازی است. حال اگر آن گونه که گاهی گفته میشود، برخی از خودروسازان و یا قطعه سازان، قطعاتشان را از چین وارد نمایند، معنی ضمنیاش آن است که لوکوموتیو اصلی به تنهایی حرکت میکند.
مهندس ملکی مدیریت مهندسی شرکت حمیدصنعت نسبت به کاهش هزینه تمام شده تولید باک فلزی نسبت به باک پلیمری خاطر نشان ساخت: این حق مردم است که بدانند گاه با تغییر طرح یک قطعه میتوان قیمت را کاهش داد، بدون این که کیفیت خدشهدار شود. در باک خودرو با تغییر طرح از باک پلیمری به باک فلزی، در خودروی پژو 405 حدود 80 هزار تومان میتوان از قیمت تمام شده خودرو کاست. این اختلاف زیاد است و چنان چه پمپ In Tank نیز در این مجموعه استفاده شود این کاهش قیمت به 100 هزار تومان خواهد رسید.
در صنعت خودروسازی داخلی، به جرات میتوان گفت، پیشرفتهترین و با کیفیتترین خودروی ساخت داخل، رنو 90 است. در این خودرو باک سوخت از نوع فلزی است. شرکت رنو در ابتدا خودروهای لوگان را با باک پلیمری وارد نمود اما پس از بررسی به این نتیجه رسید که با توجه به شرایط محیطی و بومی ایران، باک پلیمری لازم نیست و باک تندر فلزی شد. پس باید خیر و صلاح کشور هم در طراحیها، لحاظ گردد و همچنین خودرو برای مشتری نهایی گران تمام نشود. مواد پلیاتیلن خاص باک پلیمری به خاطر این که تنها دو کمپانی توتال و بازل، آن را تولید میکنند از اروپا گران وارد میشود. وقتی که پلیاتیلن تولیدی در ایران کیلویی پنج هزار تومان است ولی مواد باک را باید کیلویی 15 هزار تومان خریداری کرد، راه دیگری باقی نمیماند و مشتری و رقیب هم کاری از دستشان بر نمیآید.
ایشان در ادامه به موضوع مهم محیط زیست پرداخته و بیان داشتند: از دیدگاه زیستمحیطی، دو جنبه باید در نظر گرفته شود. یکی انتشار یا نفوذ بخار بنزین به اتمسفر و دیگری بحث بازیافت است.
در زمینه نفوذ مواد و آلایندگی سختگیرانهترین استاندارد زیستمحیطی دنیا، استانداردهای ایالت کالیفرنیا در امریکاست. مثلاً در استاندارد یورو 4 اجازه انتشار سوخت دو گرم در 24 ساعت است ولی در استاندارد ایالت کالیفرنیا مقدار مجاز نفوذ سوخت، 0.5 گرم در 72 ساعت. یعنی چندین برابر سختگیرانهتر است. در این حالت تنها باکهای فلزی قادر به گذراندن این استاندارد سختگیرانه هستند. در باک پلیمری برای آن که آلایندگی، نزدیک به صفر برسد باید تعداد لایهها را بیشتر و بیشتر نمود. بخشی از استاندارد با عنوان، partial zero emission، الزام به کاهش آلایندگی تا نزدیک صفر دارد که این امر به خودی خود قیمت را بیشتر میکند. در فرآیند تولید یک باک پلیمری، با افزایش تعداد لایهها، قیمت افزایش یافته و بازیافت آن هم سختتر میشود. پس از این نظر نیز باک فلزی قابلیت انطباق با استاندارد یورو 6 به بالا را هم دارد.
و اما از نقطه نظر بازیافت، پلیاتیلن کراسلینک شده، قابلیت بازگشت به محیط زیست را به راحتی ندارد. در اروپا حدود 303 میلیون خودرو با باک پلاستیکی وجود دارد که دیگر نمیتوان آنها را به راحتی بازیافت نمود. این تعداد باک معادل شش برابر قطر کره زمین است. باک پلاستیکی به سادگی بازیافت نمیشود، ولی باک فلزی را به عنوان قراضه میتوان دوباره و صدباره در کوره ذوب نمود. فلز را به هر تعداد بار میتوان بازیافت کرد.
پس از هر دو دیدگاه زیست محیطیِ آلایندگی و بازیافت، باک پلیمری دشمن محیط زیست است.
در اروپا بنا به مزیت رقابتی تولید کنندگانی چون بازل سوییسی و توتال فرانسوی از باک پلیمری استفاده شده است ولی در کره و ژاپن به دلیل برتری در تولید ورق از باک فلزی استفاده شده است. جالب آن است که هیوندایی که در کشور کره جنوبی خودرو را با باک فلزی تولید میکند، وقتی در اروپا سایت تولید خودرو احداث میکند از باک پلیمری بهره میبرد.
چگونگی طراحی آزمونها برای قطعاتی که در شرکت حمیدصنعت فرد بازطراحی میشوند
مهندس ملکی در خصوص نحوه طراحی آزمونهای سیستم سوخترسانی به منظور برآوردهسازی الزامات استانداردهای مورد نظر به این نکته اشاره کردند که در سیستم سوخترسانی، یک قطعه مرتبط باید آزمون عملکردی استاندارد و الزامات دولتی را بگذراند. به عنوان نمونه آزمونهای شِد (Shed)، آزمون آلایندگی گازهای منتشره و تطابق تولید (COP) و سایر آزمونها باید انجام شود. در آزمون شِد، محدوده مجاز میزان نفوذ هیدروکربن از ساختار خودرو به بیرون تعیین میشود. الان در ایران بر اساس استاندارد یورو 4، میزان مجاز نفوذ هیدروربن دو گرم در 24 ساعت مجاز است. در استاندارد یورو 2 این عدد دو گرم در دو ساعت بود. از این نظر استانداردهای یورو 5 و یورو 6 هم مثل یورو 4 هستند. ولی در استاندارد کالیفرنیا نیم گرم در 72 ساعت محدوده مجاز آلایندگی است. پس باید در واقع سیستم سوخترسانی و در نتیجه آزمونهای مربوطه به گونهای طراحی شوند که استانداردهای ملی، دولتی و الزامات خودروساز برآورده شوند. در تست (cop) میزان نشتی مجاز از کل سیستم سوخترسانی در 5 دقیقه زیر ده میلیمتر تعریف شده و بر اساس آن تست مرجع، در واقع تست کل مجموعه مشخص میگردد. در هنگام تغییر طرح قطعه، بر مبنای عملکرد قطعه و شرایط نرمال و شرایط جدیدی که برای قطعه بر اساس مواد و طرح جدید اتفاق افتاده، آزمونهای جدید مورد نیاز تبیین میشوند به گونهای که، شرایط عملکردی و دوام قطعه را ثابت کند تا در کوتاه مدت و بلندمدت براساس شرایط مختلف آب و هوایی، محیطی و کارکردی، عملکرد مناسبی داشته باشد. بخش عمده ای از فعالیت پرسنل مهندسی در شرکت حمید صنعت، طراحی این آزمونهاست و به همین منظور از مراجع مختلف استفاده میشود.
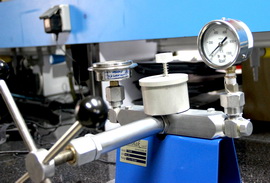 |
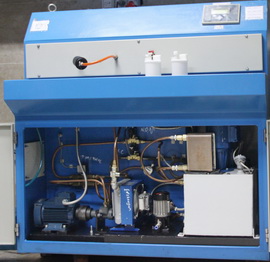
دستگاه آزمون کارایی فیلتر بنزین |
به عنوان نمونه قطعه براکت رادیاتور، که حدود پنج سال پیش در شرکت حمید صنعت تغییر طرح داده شد، یک قطعه فلزی- لاستیکی بود که به پلیمر- لاستیک تغییر یافت. در تست پلن قطعه اولیه، لاستیک فلز، از آنجا که در ابتدا قطعه فلزی بود، هیچ آزمون حرارتی در مدارک تست پلن آن تعریف نشده بود. بدیهی است که با تغییر طرح، نیاز به مشخص شدن شرایط آزمون جدید وجود داشت و از همین رو، برای تعریف الزامات و مشخصات آزمون قطعه جدید، پلیمری-لاستیکی، از قطعات دیگر موتور که در همان شرایط کار میکردند الگوبرداری شد و شرایط آزمونهای حرارتی- برودتی جدید به آزمونهای قطعه جدید در تست پلن مربوطه اضافه شد. همچنین بنا به ماهیت فلزی قطعه پیش از تغییر طرح، آزمون رنگ در تست پلن تعریف شده بود ولی در قطعه جدید نیازی به آن آزمون وجود نداشت و در نتیجه آزمون رنگ از تست پلن قطعه جدید حذف گردید. به همین منوال آزمون خوردگی از تست پلن قطعه خارج شد.
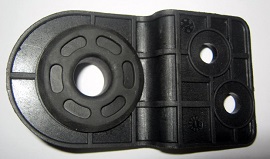
براکت پلیمری رادیاتور تیبا |
بدیهی است در این زمینه با خودروساز هم هماهنگیهای لازم انجام میشود تا در نهایت آن چیزی که به وجود میآید، هم آرامش مشتری و هم آسودگی خیال طراح اصلی را به ارمغان آورد، تا قطعه در آینده دچار مشکل نشود. تاکنون هشت میلیون عدد از فیلتری که در شرکت حمیدصنعت از فلزی به پلیمری تبدیل شده، چهار میلیون عدد از اولین لوله پرکنی که از فلزی به پلیمری تبدیل شده و سه میلیون عدد از براکت رادیاتور طراحی شده در شرکت حمیدصنعت، بر روی خودروها مونتاژ شدهاند و خوشبختانه هیچ مشکل کیفی و حتی کمی هم تاکنون گزارش نشده است.
گاه تغییر طرح از پلیمر به پلیمر است. مثلاً در قطعه فیلتر که طبق پیشنهاد شرکت حمیدصنعت از بیرون باک به داخل باک انتقال یافت، مواد پلیمر در هر دو فیلتر استفاده شده است ولی شکل قطعه عوض شد. دو عدد لوله گرانقیمت و چهار عدد رابط اتصال حذف گردید. هر یک عدد نقطه اتصال در مسیر سوخت به مثابه یک نقطه مرگ است و همیشه آن نقطه می تواند خطرزا باشد. هر یک نقطه اتصال کمتر یک کار بزرگ در راستای ایمن کردن خودرو است.